Key Points for Selecting Granite Surface Plates: Matching Dimensions, Thickness, and Machining Processes to Requirements
Author:hxrtools Time:2025-05-20 14:29:03 Click:136
In the process of the precision manufacturing industry moving towards high-quality development, high-precision measurement platforms have become key equipment for ensuring product quality. Granite surface plates, with their unique properties, stand out among platforms made of various materials and are highly favored. However, selecting a granite surface plate with appropriate dimensions, thickness, and machining processes according to actual needs is a challenge faced by many users.
I.Introduction: The Industry Value of Granite Surface Plates
1.1 Growing Demand Trend for High-Precision Measurement Platforms in the Precision Manufacturing Industry
With the rapid development of precision manufacturing industries such as aerospace, electronic information, and automotive manufacturing, the requirements for the machining accuracy of components and product quality are continuously escalating. High-precision measurement platforms, as crucial tools for ensuring dimensional accuracy and geometric tolerances of products, are witnessing a sustained increase in market demand. Traditional measuring tools can no longer meet the increasingly stringent precision requirements of the industry, making high-precision and high-stability measurement platforms an indispensable necessity.
1.2 The Core Advantages of Granite Surface Plates over Other Materials
Compared with platforms made of cast iron, steel, and other materials, granite surface plates have inherent advantages. Granite is materially stable, less susceptible to changes in temperature and humidity, and can maintain high precision over a long period. It has high hardness and strong wear resistance, resulting in a long service life. Moreover, its dense material and non-magnetic properties prevent interference with precision measurements. These characteristics make granite surface plates the first choice for applications such as high-precision measurement and precision marking.
1.3 The Core of This Article: Analysis of Key Selection Points for Dimensions, Thickness, and Machining Processes
This article focuses on the dimensions, thickness, and machining processes of granite surface plates, providing an in-depth analysis of how to match them according to actual usage requirements, helping users avoid selection pitfalls and choose the most suitable products.
II.Basic Understanding of Granite Surface Plates
2.1 Device Definition and Functional Overview
A granite surface plate is a high-precision planar reference instrument made from natural granite through processes such as cutting, grinding, and polishing. Its main function is to provide a stable and precise planar reference for precision measurement, mechanical processing, instrument calibration, and other work, ensuring the accuracy and reliability of measurement and processing results. In mechanical manufacturing, it is used to detect the flatness and straightness of components; in scientific research, it provides a reference plane for the installation and debugging of precision instruments.
2.2 Core Composition Characteristics
Physical and Chemical Properties of Granite: Granite is an igneous rock with high hardness and density. It has a low coefficient of thermal expansion, making it less affected by changes in ambient temperature and ensuring dimensional stability of the platform under different temperature conditions. It is chemically stable, highly corrosion-resistant, and not prone to rusting or oxidation, allowing it to maintain surface precision over a long period.
Relationship Between Platform Structural Design and Functional Realization: The structural design of the platform, such as the shape of the working surface and the layout of support feet, directly affects its load-bearing capacity and stability. A reasonable structural design ensures minimal deformation of the working surface when the platform is loaded with workpieces, thereby guaranteeing measurement and processing precision.
2.3 Mainstream Product Classifications
Classification by Precision Grade: Common grades include Grade 00, Grade 0, and Grade 1. Grade 00 has the highest precision and is suitable for ultra-precision measurement and calibration. Grade 0 is of slightly lower precision but can still meet high-precision requirements such as precision instrument manufacturing and metrological inspection. Grade 1 is suitable for general-precision measurement and marking work.
Classification by Purpose: They are divided into measuring, marking, and assembly types. Measuring plates have high working surface precision and are used for accurate measurements. Marking plates focus on the wear resistance of the working surface for easy marking of workpieces. Assembly plates have strong load-bearing capacity and are used for the assembly and debugging of mechanical components.
2.4 Analysis of Key Technical Parameters
Flatness: Refers to the flatness of the platform's working surface and is an important indicator for measuring platform precision. The higher the flatness, the flatter the working surface, and the smaller the measurement error.
Surface Roughness: Reflects the microscopic geometric shape error of the platform's working surface. A smaller value indicates a smoother surface, better contact with workpieces, and higher measurement precision.
Load-Bearing Capacity: Indicates the maximum weight the platform can withstand. When selecting, it is necessary to consider the weight and distribution of workpieces actually loaded on the platform to ensure that the platform does not deform due to overloading.
Hardness: The high hardness of granite enables it to resist friction and impacts from workpieces, maintaining working surface precision. The higher the hardness, the stronger the wear resistance and durability of the platform.
III.Key Points for Selecting Dimensions, Thickness, and Machining Processes
3.1 Key Points for Matching Dimensions to Requirements
Principles for Selecting Platform Dimensions Based on the Size of Measured Workpieces: The platform dimensions should be slightly larger than the maximum outline dimensions of the workpiece to be measured, ensuring that the workpiece can be fully placed on the platform's working surface with some operating space left around it for the use of measuring tools and personnel operations.
Methods for Considering Operating Space and Future Expansion Needs: In addition to meeting current workpiece measurement requirements, consideration should also be given to possible future scenarios involving larger-sized workpieces or simultaneous measurement of multiple workpieces, with appropriate space reserved. Additionally, if the enterprise has business expansion plans, choosing a larger-sized platform can reduce the cost of later equipment replacement.
3.2 Key Factors in Thickness Selection
Correspondence Between Load-Bearing Weight and Platform Thickness: Generally, the greater the load-bearing weight of the platform, the thicker it needs to be. Thicker platforms have better rigidity and stability, effectively reducing deformation when loaded. When selecting, it is necessary to reasonably choose according to the actual load-bearing weight and refer to the load-bearing-thickness parameter table provided by the manufacturer.
Differentiated Strategies for Thickness Selection in Different Usage Scenarios: For high-precision measurement scenarios, even with relatively light load-bearing weights, a platform with an appropriate thickness should be selected to ensure stability. For scenarios such as marking and assembly, which have relatively lower precision requirements but higher load-bearing weights, priority should be given to the load-bearing capacity of the platform, and a thicker platform should be selected.
3.3 Matching Machining Processes to Requirements
Impact of Machining Processes Such as Grinding and Scraping on Platform Precision: The grinding process uses grinding tools and abrasives to finely machine the platform's working surface, improving surface flatness and smoothness. The scraping process involves manual scraping to further correct microscopic errors on the platform's working surface, achieving higher flatness precision. Different machining processes are suitable for platforms with different precision requirements. Grinding is commonly used for the processing of general-precision platforms, while scraping is often used for the finishing of high-precision platforms.
Methods for Selecting Machining Processes Based on Usage Precision Requirements: If the usage scenario has high precision requirements, such as metrological inspection and precision instrument manufacturing, a platform processed by the scraping process should be selected. For general-precision measurement and marking work, a platform processed by the grinding process can meet the requirements. At the same time, attention should also be paid to the fineness of the machining process, such as the particle size of grinding and the number of scraping points.
3.4 Comprehensive Matching Strategies
Overall Selection Approach Considering Factors Such as Budget and Usage Frequency: When selecting, it is necessary to comprehensively consider factors such as budget cost and usage frequency. If the budget is limited and the usage frequency is not high, a platform that meets basic precision requirements with appropriate dimensions and thickness can be selected. For scenarios with frequent use and high precision requirements, it is appropriate to increase the budget and choose high-quality, high-performance products.
Avoiding Common Pitfalls Such as Excessively Large or Small Dimensions and Unreasonable Thickness: An excessively large platform will occupy too much space and increase costs; an excessively small platform will not meet measurement requirements. Improper thickness selection, with a platform that is too thin being prone to deformation and affecting precision, and a platform that is too thick increasing costs and handling difficulty, should be avoided during selection. Careful assessment is needed to prevent falling into these pitfalls.
IV. Selection and Usage Recommendations
4.1 Supplier Selection and Quality Judgment
Key Points for Evaluating Suppliers' Production Qualifications and Technical Strengths: Prioritize suppliers with relevant production qualification certifications, such as quality management system certifications. Understand their production equipment, technical teams, and R&D capabilities. The production technology level can be assessed by visiting the supplier's production workshop and process flow.
Practical Methods for Distinguishing Product Quality: Observe whether the platform surface is flat and smooth, without defects such as cracks or sand holes. Check the platform's precision inspection report to confirm that its precision indicators meet the requirements. You can also tap the platform and judge the material density based on the sound; a clear sound indicates better material quality.
4.2 Key Inspection Items and Standards During Delivery Acceptance
Key Inspection Items and Standards During Delivery Acceptance: Upon arrival, check whether the platform's appearance is intact and whether the accessories are complete. Use professional measuring tools to retest key parameters such as the platform's flatness and dimensions to ensure they are consistent with the contract.
Environmental Requirements for Platform Installation and Correct Installation Steps: Granite surface plates should be installed in a dry, vibration-free, and temperature-stable environment. During installation, first adjust the support feet to a horizontal state, then place the platform steadily, and use a level gauge for fine adjustment to ensure the platform is in a horizontal position.
4.3 Daily Maintenance and Care Tips
Maintenance Methods for Extending the Service Life of Granite Surface Plates: Regularly clean the platform's working surface with a clean soft cloth and avoid using corrosive cleaners. Prevent the platform from being impacted by heavy objects and scratched by sharp objects. When not in use, cover it with a dust cover to prevent dust and debris from contaminating the working surface.
Common Problem Prevention and Simple Fault Handling Measures: To prevent platform deformation, avoid overloading and long-term local stress. If slight scratches are found on the platform surface, professional grinding tools can be used for repair. If precision degradation occurs, professional personnel should be contacted for calibration and maintenance.
V. Industry Trends and Future Outlook
5.1 Technological Innovation Directions
Development Trends and Impacts of High-Precision Machining Technologies: In the future, the machining technology of granite surface plates will move towards even higher precision. For example, the adoption of nanometer-level grinding technology and automated scraping equipment will further improve the flatness and surface quality of platforms, meeting the needs of ultra-precision manufacturing fields.
Integration Trends of Intelligent Detection and Calibration Functions: With the development of the Internet of Things and sensor technologies, granite surface plates will integrate intelligent detection modules that can monitor the platform's precision status in real-time and automatically perform calibration, improving measurement accuracy and efficiency.
5.2 Changes in Market Demand
New Characteristics of Demand for Granite Surface Plates in Emerging Industries: With the rise of emerging industries such as new energy vehicles and semiconductors, new requirements have been put forward for the precision, dimensions, and functions of granite surface plates. For example, there will be an increasing demand for smaller and more customized platforms.
Growth Trends and Responses to Personalized Customization Demands: Users' personalized demands for granite surface plates are growing. Suppliers need to strengthen their R&D capabilities and provide customized services, designing and producing platforms that meet specific usage scenarios according to customers' special requirements.
5.3 Green Environmental Protection and Sustainable Development
Application Trends of Environmental Protection Technologies in the Production Process: In the production process of granite surface plates, more environmentally friendly machining processes and materials will be adopted to reduce the generation of waste water, waste gas, and waste residues and minimize environmental impacts.
Development Directions for Material Recycling and Reuse: Explore recycling and reuse technologies for granite waste, such as processing waste materials into building materials, to improve resource utilization and achieve sustainable development in the industry.
VI. Conclusion: Scientific Selection to Unleash the Platform's Value
The dimensions, thickness, and machining processes of granite surface plates are key factors affecting their performance and applicability. Through the analysis of selection points in this article, it is hoped that users can make scientific and reasonable decisions when selecting, combined with their own actual needs. At the same time, correct usage and maintenance methods can also fully leverage the performance advantages of granite surface plates, providing reliable guarantees for precision manufacturing work. If you still have questions during the selection process, welcome to further explore more professional content to find the granite surface plate that best suits your needs.
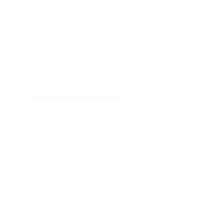
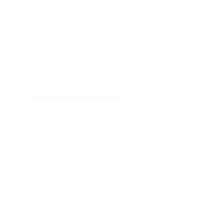
Whatapp:+86 18932785670
Tel:+86 18932785670
E-mail:project@haoranmj.com
Add:Across from Sanjing Distillery on Road 4, Botou Economic Development Zone, Cangzhou City, Hebei Province