A Comprehensive Guide to Purchasing Welding Workbenches: Avoid Pitfalls and Choose the Right Equipment from Materials to Functions
Author:hxrtools Time:2025-05-27 09:02:07 Click:103
In modern industrial production, welding, as a crucial processing technique, plays a decisive role in product manufacturing with respect to operational efficiency and quality. The welding workbench, as the fundamental equipment for welding operations, directly impacts welding results through its performance. Given the wide variety of welding workbenches available on the market, each with distinct materials and functions, how can one select the most suitable equipment from the plethora of options?
I. Introduction: The Industry Value of Welding Workbenches
1.1 Development Trends in the Welding Industry and Equipment Demand
As the manufacturing sector advances towards automation and precision, welding processes find increasingly widespread applications in fields such as automotive manufacturing, steel structure engineering, and mechanical machining. Traditional simple welding platforms can no longer meet the demands for high-precision and high-efficiency welding. Consequently, the market demand for specialized and multifunctional welding workbenches continues to surge.
1.2 Core Advantages of High-Quality Welding Workbenches
Compared to ordinary work platforms, professional welding workbenches offer superior stability, diverse functions, and comprehensive safety protections. They not only provide stable support for welding operations but also optimize the welding process through functional designs, reducing operator fatigue and enhancing welding quality and production efficiency.
1.3 Core Focus of This Article: Key Considerations for Material and Function Selection
This article delves into the material characteristics and functional configurations of welding workbenches, providing an in-depth analysis of the considerations during the purchasing process to help users avoid selection pitfalls and choose equipment that meets their actual needs.
II. Basic Understanding of Welding Workbenches
2.1 Device Definition and Functional Overview
A welding workbench is a specialized platform designed for welding operations, primarily used to support welding workpieces, fix welding positions, and provide storage space for welding tools. Its functions encompass workpiece positioning, welding operation assistance, and safety protection, making it an essential piece of equipment for ensuring the smooth progress of welding operations.
2.2 Core Component Characteristics
Frame Structure: The frames of welding workbenches are typically constructed from welded steel. The overall strength and stability of the workbench are determined by the rational design of the frame and the welding process employed.
Work Surface Material: The work surface directly contacts the welding workpieces and tools. It must possess properties such as high-temperature resistance, wear resistance, and deformation resistance to withstand the high temperatures and mechanical friction encountered during welding.
2.3 Mainstream Product Classifications
By Purpose: Classified into general-purpose welding workbenches and specialized welding workbenches. General-purpose workbenches are suitable for a variety of welding scenarios, while specialized workbenches are designed for specific welding processes or industries, such as automotive welding-specific workbenches or stainless steel welding workbenches.
By Structure: Includes stationary welding workbenches and mobile welding workbenches. Stationary workbenches offer strong stability and are suitable for fixed workstation operations, while mobile workbenches are equipped with casters for easy movement and adjustment of work positions.
2.4 Analysis of Key Technical Parameters
Load-Bearing Capacity: Reflects the maximum weight that the workbench can withstand. It is essential to select a workbench with an appropriate load-bearing specification based on the weight of the welding workpieces to prevent deformation due to overloading.
Work Surface Flatness: The flatness of the work surface affects the positioning accuracy of workpieces during welding. Higher flatness contributes to better welding quality.
High-Temperature Resistance: Welding processes generate high temperatures, so the workbench must possess good high-temperature resistance to prevent deformation or damage to the work surface due to heat.
III. Key Considerations for Material and Function Selection
3.1 Core Elements of Material Selection
Steel Type: Common steel types include ordinary carbon steel, stainless steel, and alloy steel. Ordinary carbon steel is cost-effective and suitable for general welding operations. Stainless steel is corrosion-resistant and suitable for welding workpieces with high cleanliness requirements. Alloy steel offers high strength and toughness, making it suitable for heavy-duty welding scenarios.
Surface Treatment Process: The workbench surface typically undergoes anti-rust treatments such as painting or galvanizing. A high-quality surface treatment process not only enhances anti-rust capabilities but also improves surface wear resistance, extending the workbench's service life.
3.2 Functional Configuration to Meet Demands
Positioning and Clamping Functions: Equipped with structures such as T-slots and bolt holes, the workbench can be paired with fixtures to achieve rapid positioning and fixation of workpieces, improving welding efficiency. Some workbenches also feature adjustable positioning devices to accommodate welding needs for workpieces of different shapes.
Auxiliary Function Designs: Such as tool hangers, power sockets, and exhaust ports. Tool hangers facilitate the placement of welding tools. Power sockets provide convenient access to electricity for welding equipment. Exhaust ports can be connected to exhaust systems to promptly remove harmful gases generated during welding, improving the working environment.
3.3 Comprehensive Matching Strategies
Combining Budget with Usage Scenarios: With a limited budget, prioritize workbenches that meet basic functional requirements. For high-precision and high-frequency welding operations, it may be appropriate to increase the budget to select equipment with superior materials and rich functions.
Avoiding Functional Redundancy or Deficiency: Based on actual welding process requirements, reasonably select functional configurations to avoid increasing costs due to overly complex functions or affecting welding operations due to functional deficiencies.
IV. Selection and Usage Recommendations
4.1 Supplier Selection and Quality Assessment
Evaluating Production Qualifications and Technical Strength: Prioritize suppliers with relevant production qualifications and quality management system certifications. Understand their production equipment and process levels to ensure stable product quality.
Discerning Product Quality: Observe whether the workbench frame is firmly welded, with no false welds or missed welds. Check if the work surface is flat, with no cracks or blowholes. Test the flexibility and reliability of each functional component.
4.2 Key Items for Acceptance and Installation Notes
Key Items for Arrival Acceptance: Verify whether the workbench dimensions, load-bearing capacity, and other parameters are consistent with the contract. Check if all accessories are complete. Use a level to detect the workbench's levelness.
Installation Environment and Steps: Install the workbench in a dry, well-ventilated, and spacious location to ensure a flat installation surface. Follow the instructions to correctly install each component. For mobile workbenches, check if the caster locking function is normal.
4.3 Daily Maintenance and Care Tips
Maintenance Methods to Extend Service Life: Regularly clean welding slag and oil stains from the workbench surface to prevent corrosion. Lubricate movable parts to prevent rust and jamming. Avoid placing excessively heavy or sharp objects on the workbench to prevent damage to the work surface.
Preventive Measures for Common Problems: Avoid prolonged localized heating during welding to prevent deformation of the work surface due to high temperatures. Regularly inspect the structural stability of the workbench and address any issues promptly.
V. Industry Trends and Future Outlook
5.1 Directions for Technological Innovation
Intelligent Function Upgrades: In the future, welding workbenches will incorporate intelligent control systems to achieve functions such as automatic workpiece positioning and automatic adjustment of welding parameters, enhancing the level of welding automation.
New Material Applications: Research and development of new high-temperature-resistant and high-strength materials will improve workbench performance while reducing equipment weight, facilitating movement and operation.
5.2 Changes in Market Demand
Growing Demand for Personalized Customization: Different industries and welding processes have varying requirements for workbenches. Personalized customization will become an important trend to meet diverse market demands.
Increasing Requirements for Green and Environmental Protection: The market is imposing increasingly stringent environmental performance requirements on welding workbenches. Equipment with low noise, low energy consumption, and easy recyclability will be more favored.
5.3 Evolution of Market Competition Patterns
As market competition intensifies, enterprises will place greater emphasis on product research and development and innovation to enhance product quality and service levels. Meanwhile, brand effects will become more pronounced, and suppliers with brand advantages will occupy a favorable position in market competition.
VI. Conclusion: Scientific Selection for Efficient Operations
The materials and functions of welding workbenches directly impact the efficiency and quality of welding operations. Through a detailed analysis of the selection considerations in this article, it is hoped that users can avoid pitfalls during the purchasing process and select suitable equipment. In practical use, correctly maintain and care for the workbench to fully leverage its performance advantages and provide reliable guarantees for welding production.
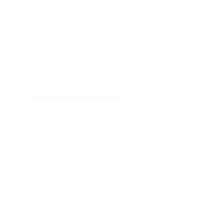
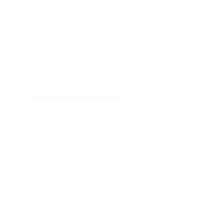
Whatapp:+86 18932785670
Tel:+86 18932785670
E-mail:project@haoranmj.com
Add:Across from Sanjing Distillery on Road 4, Botou Economic Development Zone, Cangzhou City, Hebei Province