Secrets of Daily Cleaning and Maintenance for Welding Workbenches: 5 Key Steps to Extend Service Life
Author:hxrtools Time:2025-05-29 09:35:21 Click:101
In welding operations, the welding workbench serves as a crucial piece of foundational equipment to ensure smooth production. The stability of its performance directly impacts welding quality and work efficiency. However, during prolonged use, factors such as high temperatures, welding spatter, and metal debris can cause damage to the workbench. Mastering scientific cleaning and maintenance methods can effectively extend the service life of a welding workbench.
I. Introduction: The Importance of Welding Workbench Maintenance
1.1 Impact of Welding Operations on the Workbench
The high temperatures, sparks, and flying welding spatter generated during the welding process, along with the friction from prolonged contact with metal workpieces, can cause varying degrees of damage to the surface and structure of the welding workbench. If not maintained promptly, this can lead to a decline in the workbench's precision and structural stability.
1.2 Core Advantages of Proper Maintenance
Regular cleaning and maintenance of the welding workbench not only keep its appearance tidy but also effectively reduce equipment wear, prevent structural deformation, and maintain the workbench's precision and load-bearing capacity. This, in turn, lowers maintenance costs and ensures efficient and stable welding operations.
1.3 Core Focus of This Article: Analysis of 5 Key Maintenance Steps
This article focuses on the five key steps in the daily cleaning and maintenance of welding workbenches, providing detailed explanations of operation methods and precautions to help users master scientific maintenance techniques and extend the service life of their equipment.
II. Basic Understanding of Welding Workbenches
2.1 Device Definition and Functional Overview
A welding workbench is a specialized platform designed for welding operations. It is used to support and fix welding workpieces, provide space for welding operations, and can be equipped with auxiliary tools and equipment to facilitate the smooth conduct of welding work.
2.2 Core Component Characteristics
Frame Structure: Typically constructed from welded steel, its strength and stability determine the workbench's load-bearing capacity.
Work Surface: Directly contacts welding workpieces and tools and is generally made of high-temperature-resistant and wear-resistant materials, such as cast iron or special steels.
2.3 Mainstream Product Classifications
By Purpose: Classified into general-purpose welding workbenches and specialized welding workbenches. The former are suitable for a variety of welding scenarios, while the latter are designed for specific welding processes.
By Structure: Includes stationary and mobile welding workbenches, with slightly different maintenance priorities for different structures.
2.4 Correlation Between Key Technical Parameters and Maintenance
Load-Bearing Capacity: During maintenance, it is necessary to avoid overloading to prevent frame deformation that could affect the workbench's performance.
Work Surface Flatness: Regularly inspect and maintain it to ensure the work surface remains flat and guarantee welding precision.
III. 5 Key Steps to Extend Service Life
3.1 Step 1: Daily Cleaning and Dust Removal
Cleaning Frequency: After each welding operation, promptly clean metal debris, welding spatter, dust, and other impurities from the workbench surface.
Cleaning Tools and Methods: Use tools such as brushes and vacuum cleaners to gently sweep the surface. For stubborn stains, use a clean soft cloth with a neutral cleaner to wipe, avoiding the use of sharp tools to scrape the work surface.
3.2 Step 2: Removal of Welding Spatter and Splatter
Timing of Removal: After the welding spatter has cooled, promptly clean it to prevent adhesion to the workbench surface.
Operation Methods: Use tools such as spatulas and copper brushes to carefully scrape off the welding spatter, avoiding damage to the workbench surface. For splatter that is difficult to remove, lightly sand it with sandpaper, but be careful to control the force to prevent excessive wear.
3.3 Step 3: Rust Prevention Treatment
Rust-Prone Areas: Focus on areas of the workbench that are prone to rusting, such as the frame, bolts, and welding points.
Treatment Methods: Regularly apply anti-rust grease or anti-rust paint to form a protective film. If local rusting is found, first use sandpaper to grind off the rust before applying rust prevention treatment.
3.4 Step 4: Inspection and Tightening
Inspection Items: Regularly check the welding areas of the workbench frame for cracks or weld separation, whether the bolts are loose, and whether the connections between various components are secure.
Tightening Operations: Use a wrench to tighten loose bolts to the specified torque. If damage to the welding areas is found, it should be promptly repaired or handled by a professional.
3.5 Step 5: Regular Deep Maintenance
Maintenance Cycle: Conduct a deep maintenance every 3 - 6 months, depending on the frequency of workbench use.
Maintenance Content: Thoroughly clean the workbench, check the flatness and precision of the work surface; lubricate movable parts (such as the casters of mobile workbenches); evaluate the overall structural stability of the workbench and, if necessary, perform calibration or repairs.
IV. Maintenance Precautions and Handling of Common Problems
4.1 Maintenance Precautions
Avoid Corrosive Cleaners: Prevent cleaners from causing corrosion to the workbench surface and structure.
Prevent Excessive Force: During cleaning and maintenance, avoid using excessive force to prevent damage to the workbench.
Wear Protective Equipment: Wear gloves, goggles, and other protective gear during operations to ensure personal safety.
4.2 Handling of Common Problems
Work Surface Wear: If minor wear is found on the work surface, it can be repaired by grinding. For severe wear, contact a professional for handling.
Frame Deformation: Minor deformations can be corrected. For severe deformations, replace the damaged components to ensure the safe use of the workbench.
V. Industry Trends and Upgrades in Maintenance Concepts
5.1 Intelligent Maintenance Reminders
In the future, welding workbenches may integrate sensors to automatically monitor equipment status and promptly prompt maintenance needs, making maintenance work more intelligent and precise.
5.2 Application of Green Maintenance Materials
With the increasing environmental protection requirements, environmentally friendly cleaners, rust preventives, and other maintenance materials will be more widely used to protect equipment while reducing environmental impact.
5.3 Trend Towards Preventive Maintenance
Shift from passive repairs to active prevention. Through regular comprehensive inspections and maintenance, potential problems can be identified in advance, reducing the risk of equipment failures and improving production efficiency.
VI. Conclusion: Scientific Maintenance for Continuous Production Support
Daily cleaning and maintenance of welding workbenches are key to ensuring their performance and extending their service life. By mastering these five key steps and performing regular maintenance, equipment failures can be effectively reduced, maintenance costs lowered, and stable and reliable support provided for welding operations.
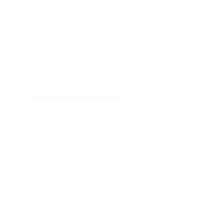
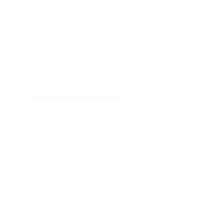
Whatapp:+86 18932785670
Tel:+86 18932785670
E-mail:project@haoranmj.com
Add:Across from Sanjing Distillery on Road 4, Botou Economic Development Zone, Cangzhou City, Hebei Province