A Comprehensive Guide to Purchasing Cast Iron Platforms: Key Considerations from Material to Precision
Author:hxrtools Time:2025-06-02 13:45:49 Click:71
In fields such as mechanical manufacturing and precision measurement, cast iron platforms serve as indispensable foundational equipment. Their performance directly impacts production quality and efficiency. Faced with a wide variety of cast iron platforms on the market, numerous factors, from material characteristics to precision grades, require careful consideration.
I. Introduction: The Industrial Value of Cast Iron Platforms
1.1 Manufacturing Upgrades Drive Equipment Demand
As the manufacturing industry advances towards high-end and precision-oriented development, sectors like mechanical processing, mold manufacturing, and instrument calibration have placed higher demands on the precision and stability of basic processing platforms. Cast iron platforms, with their excellent load-bearing performance and reliable benchmarking capabilities, have become key equipment for ensuring smooth production processes, leading to a continuous increase in market demand.
1.2 Core Competitive Advantages of Cast Iron Platforms
Compared to platforms made of other materials, cast iron platforms stand out due to their good casting properties, superior shock absorption, and excellent wear resistance. The internal graphite structure effectively buffers processing vibrations, while the high hardness of the material resists long-term friction and wear, maintaining stability under complex working conditions and achieving a balance between cost and performance.
1.3 Focus of This Article: Analysis of Key Parameters for Purchase
This article focuses on the core parameters of cast iron platforms, such as material characteristics and precision grades, providing an in-depth analysis of how each element affects platform performance. It offers a systematic purchasing approach to help users avoid common pitfalls and make informed decisions.
II. Fundamental Knowledge of Cast Iron Platforms
2.1 Equipment Definition and Functional Overview
Cast iron platforms are planar benchmarking tools made from cast iron through casting and machining processes. They are primarily used for the measurement and calibration of workpieces, scribing and positioning, and assembly inspection, providing a stable working plane and precise benchmark for mechanical processing. They are crucial tools for ensuring processing accuracy in industrial production.
2.2 Core Component Characteristics
Cast Iron Material Properties: The flake graphite structure within cast iron imparts the platform with good vibration-damping properties, effectively absorbing vibrations and impacts during processing. Its high hardness and wear resistance make it resistant to long-term wear, maintaining the accuracy of the benchmark surface.
Platform Structural Design: Reasonable rib layout and box-type structures enhance the platform's rigidity and load-bearing capacity. Optimized structural designs can distribute load pressures, ensuring the platform remains deformation-free under heavy-load conditions.
2.3 Mainstream Product Classifications
By Precision Grade: Platforms are classified into grades such as 0, 1, and 2, with Grade 0 being the highest precision, suitable for ultra-precision measurement and calibration; Grade 1 meets the needs of precision instrument manufacturing; and Grade 2 is suitable for general mechanical processing and assembly operations.
By Purpose: Platforms include measuring platforms, scribing platforms, and assembly platforms, among others. Different types vary in precision requirements, surface treatments, and functional designs to suit different production scenarios.
2.4 Analysis of Key Technical Parameters
Flatness: Reflects the evenness of the platform's working surface and directly determines the benchmarking precision for measurement and processing. Higher flatness results in smaller processing errors and is one of the core indicators for measuring platform quality.
Load-Bearing Capacity: Determined by the platform's material, structure, and dimensions. It must be selected based on the actual weight of the workpieces, tooling and fixture weights, and the forces encountered during operation to ensure safe and stable platform operation.
Hardness: Appropriate hardness ensures the platform can resist workpiece friction and impacts while facilitating later precision restoration. The hardness value affects the platform's durability and maintenance costs.
III. Key Considerations for Material and Precision
3.1 Core Elements of Material Selection
Differences in Cast Iron Types: Common types include gray cast iron, which is low-cost and has good casting properties, suitable for general industrial applications; ductile iron, which offers high strength and toughness, making it more suitable for heavy-load or high-precision requirements; and malleable iron, which has good plasticity and is suitable for manufacturing platforms with complex structures.
Impact of Impurities and Composition: The content of impurities like sulfur and phosphorus in cast iron affects material performance. Lower impurity content leads to higher toughness and strength. Reasonable proportions of main components like carbon and silicon can optimize the platform's wear resistance and deformation resistance.
3.2 Strategies for Precision Grade Adaptation
Matching Processing Requirements: Select platforms corresponding to the actual production precision requirements. For precision part measurement, Grades 0 or 1 platforms should be chosen to ensure data accuracy; for general mechanical assembly and scribing operations, Grade 2 platforms can balance cost and performance.
Controlling Precision Redundancy: Avoid blindly pursuing excessively high precision grades that increase costs while preventing quality defects due to insufficient precision. A comprehensive judgment should be made based on the enterprise's production processes and development plans.
3.3 Comprehensive Consideration of Other Parameters
Size Specification Adaptation: Platform size should be selected based on workpiece size and operational space requirements, ensuring the workpiece can be fully placed with sufficient operational space reserved. Future business expansion needs should also be considered to avoid production limitations due to equipment size.
Surface Treatment Processes: Common surface treatments include painting, applying anti-rust oil, and bluing. Different treatment processes vary in rust and wear resistance, and should be selected based on the usage environment and frequency to extend the platform's service life.
3.4 Avoiding Common Purchase Pitfalls
Ignoring Working Condition Differences: Different industries and processing links have varying requirements for platform performance. Materials and precision should be selected based on actual working conditions to avoid a "one-size-fits-all" approach.
Overemphasis on Price: Low-cost products may have defects in material purity and processing techniques, leading to unstable precision or insufficient load-bearing capacity. Product cost-effectiveness should be comprehensively evaluated rather than relying solely on price comparisons.
IV. Purchase and Usage Recommendations
4.1 Supplier Selection and Quality Judgment
Examining Production Qualifications: Prioritize suppliers with relevant production qualifications and ISO quality management system certifications. Understand the advanced nature of their production equipment and the maturity of their processes to ensure stable and reliable product quality.
Quality Inspection Methods: Observe whether the platform surface is flat and free from casting defects like sand holes and air pores. Check the completeness of the precision inspection report. Judge material density by tapping the platform; a clear sound indicates good material quality.
4.2 Acceptance and Installation Precautions
Acceptance Items Upon Arrival: Verify that the platform's dimensions, precision grade, load-bearing capacity, and other parameters match the contract. Use a level to inspect the platform's flatness. Check that all accessories are complete and the surface is undamaged.
Installation Environment Requirements: Install the platform in a dry, flat, and vibration-free environment. Adjust the shims to level the platform, ensuring even force distribution at all support points to avoid affecting platform precision due to improper installation.
4.3 Daily Maintenance and Care Tips
Extending Service Life: Regularly clean the platform surface of iron filings and oil stains to prevent impurities from affecting precision. Avoid striking operations on the platform to prevent work surface damage. Apply anti-rust oil regularly for rust prevention.
Preventing Common Issues: Strictly control platform loads to avoid overloading. Regularly inspect the platform's structural stability and promptly address issues like frame deformation or weld cracking to ensure safe equipment operation.
V. Industry Trends and Future Outlook
5.1 Technological Innovation Directions
High-Precision Processing Upgrades: Future cast iron platforms will widely adopt advanced processes like CNC grinding and laser calibration to further enhance flatness and surface quality, meeting the stringent requirements of ultra-precision manufacturing.
Intelligent Function Expansion: Incorporate sensor technology for real-time platform status monitoring, such as load warnings and deformation detection. Combine with IoT technology to support remote monitoring and fault diagnosis, enhancing equipment intelligence.
5.2 Changes in Market Demand
Growing Demand for Customization: With the development of manufacturing sub-sectors, users have increasing personalized needs for platform size, precision, and functions. Suppliers need to strengthen their customization capabilities to meet diverse market demands.
Special Requirements from Emerging Industries: Emerging industries like new energy and semiconductors have higher requirements for cast iron platforms in terms of corrosion resistance, lightweight design, and high precision, driving product upgrades towards high performance and specialization.
5.3 Green and Environmentally Friendly Development Trends
Environmentally Friendly Production Processes: Promote green casting processes to reduce emissions of waste gas, wastewater, and waste residue during production. Use environmentally friendly coatings and anti-rust agents to lower environmental pollution.
Resource Recycling and Reuse: Strengthen research on cast iron waste recycling technologies to improve resource utilization rates, achieve sustainable industry development, and reduce enterprise production costs and environmental burdens.
VI. Conclusion: Scientific Purchase, Empowering Production
The material and precision of cast iron platforms are core elements affecting their performance, while other parameters like size and surface treatment, as well as usage scenario requirements, must also be comprehensively considered. Through this systematic purchasing guide, we hope to help you avoid purchase pitfalls and select a suitable cast iron platform. In actual use, proper maintenance, care, and standardized operations will fully leverage the platform's performance advantages, enhancing enterprise production quality and efficiency.
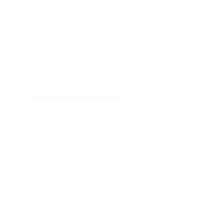
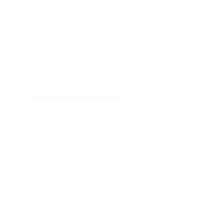
Whatapp:+86 18932785670
Tel:+86 18932785670
E-mail:project@haoranmj.com
Add:Across from Sanjing Distillery on Road 4, Botou Economic Development Zone, Cangzhou City, Hebei Province