The Application Value and Selection Strategies of Welding Workbenches in Different Industries
Author:hxrtools Time:2025-06-10 07:42:13 Click:54
I. Introduction: The Close Connection Between welding table and Industry Demands
In the modern industrial production system, welding, as the core process for metal joining, is widely applied across multiple fields. As the foundational platform for welding operations, the performance and functionality of welding table directly impact welding quality and production efficiency. Due to differences in product characteristics, process standards, and production scales across industries, the demands for welding table vary. A deep understanding of the application value of welding table in various industries and the mastery of scientific selection strategies are crucial for enterprises to enhance production efficiency and ensure product quality.
II. Machinery Manufacturing Industry: Ensuring Welding Precision for Large Components
(A) Application Value
In the machinery manufacturing industry, welding operations for large mechanical components demand extremely high precision and stability. welding table, with their robust structural designs, can withstand the weight of heavy workpieces, ensuring fixed workpiece positions during welding and reducing welding deviations caused by movement. Their height and angle adjustability features facilitate operators in adopting optimal welding postures, enhancing the welding accuracy of complex components and providing reliable guarantees for the quality and performance of mechanical products.
(B) Selection Strategy Points
When selecting, priority should be given to the workbench's load-bearing capacity, choosing types that adopt high-strength materials and reinforced frame structures. For welding large components, adjustable or heavy-duty welding table are more suitable, equipped with high-precision fixtures to meet the requirements for precise positioning and fixation of workpieces.
III. Automotive Manufacturing Sector: Meeting High-Precision Standardized Production
(A) Application Value
Automotive manufacturing pursues high precision and standardization in the welding of components, with welding table playing a pivotal role. Multi-functional integrated welding table can integrate various functional accessories, such as dedicated fixtures and tool storage systems, enabling rapid positioning and efficient welding of automotive components. The stable workbench surface ensures consistency in the welding process, guaranteeing uniform welds and meeting the dual requirements of product quality and production efficiency in automotive production lines.
(B) Selection Strategy Points
welding table with higher automation levels and precise adjustment functions should be selected. Considering the diversity of automotive components, workbenches need to accommodate workpieces of different sizes and shapes, with good surface treatment processes to prevent oil stains and metal debris residues from affecting welding quality.
IV. Metal Furniture Production: Adapting to Complex Shape Welding Needs
(A) Application Value
Metal furniture features diverse shapes and complex craftsmanship, posing high requirements for the flexibility and adaptability of welding table. Adjustable welding table can flexibly adjust height and angle according to the shape and size of furniture components, facilitating multi-angle welding. The integration of multi-functional accessories, such as fixtures with special shapes, aids in fixing complex-shaped workpieces, ensuring accurate welding positions and thus creating metal furniture products with exquisite appearances and robust structures.
(B) Selection Strategy Points
Priority should be given to welding table with high flexibility and rich accessories to cope with diverse welding needs. Meanwhile, consider the workbench's surface smoothness and wear resistance to avoid scratching furniture surfaces during welding, affecting product aesthetics and quality.
V. Shipbuilding Industry: Supporting Welding Operations for Heavy Structural Components
(A) Application Value
Shipbuilding involves the welding of numerous large and heavy structural components, imposing stringent requirements on the load-bearing capacity and stability of workbenches. Heavy-duty welding table, with their ultra-strong load-bearing capacities and robust structural designs, can firmly support ship structural components, maintaining stable performance even under simulated harsh marine operating environments, ensuring welding quality and the safety and reliability of ship structures.
(B) Selection Strategy Points
Heavy-duty welding table with high-strength materials and large load-bearing specifications must be selected, with their frame structures undergoing special reinforcement treatments. Additionally, workbenches should possess good rust and corrosion resistance to adapt to the humid and high-salinity operating environments in shipbuilding.
VI. Applications and Selection References in Other Industries
(A) Aerospace Sector
Aerospace components demand extremely high welding precision and cleanliness. When selecting, attention should be paid to the workbench's anti-static and dust-proof properties, as well as its adjustment precision, to ensure that the welding quality of micro-components meets high standards.
(B) Electronics and Electrical Appliances Industry
Welding operations for electronic and electrical products are mostly precision tasks. Small, high-precision welding table should be selected, equipped with fine adjustment devices and anti-static surface treatments to meet the special needs of electronic component welding.
VII. Summary of General Selection Principles
(A) Selection Based on Process Requirements
Select workbench types that align with the enterprise's main welding processes (such as arc welding, laser welding, etc.). For example, laser welding demands higher stability and precision from workbenches, necessitating the selection of high-precision, low-vibration workbenches.
(B) Considering Production Scale Factors
For small-scale production, workbenches with high flexibility and low costs can be selected; for large-scale batch production, workbenches with high automation levels and fast production efficiencies are required to meet capacity demands.
(C) Emphasizing Material and Process Quality
Materials determine the workbench's load-bearing capacity, durability, and stability. Prioritize high-strength, corrosion-resistant materials. Meanwhile, pay attention to the workbench's processing technology, such as welding quality and surface treatment processes, to ensure long-term stable operation of the equipment.
VIII. Conclusion: Precise Selection Unleashes Maximum Equipment Value
The application value of welding table in different industries is significant. By combining the production characteristics and needs of various industries and adopting scientific and reasonable selection strategies, the performance advantages of the equipment can be fully utilized, enhancing welding operation efficiency and quality. When selecting welding table, enterprises need to comprehensively consider factors such as process requirements, production scale, material quality, and processing technology to accurately match equipment, providing solid guarantees for production activities, thereby occupying a competitive advantage in the industry and promoting sustained industrial development.
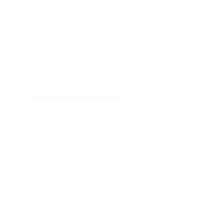
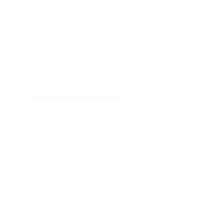
Whatapp:+86 18932785670
Tel:+86 18932785670
E-mail:project@haoranmj.com
Add:Across from Sanjing Distillery on Road 4, Botou Economic Development Zone, Cangzhou City, Hebei Province