Key Points Analysis of Customized welding table: The Crux of Meeting Personalized Welding Needs
Author:hxrtools Time:2025-06-14 15:03:21 Click:66
I. Introduction: The Necessity of Customized welding table
In welding operations, there are significant differences in production requirements, process characteristics, and workpiece types among different enterprises. General-purpose welding table often struggle to fully align with the diverse usage scenarios. Customized welding table, through targeted designs, can precisely match personalized welding needs, playing a crucial role in enhancing welding efficiency, ensuring welding quality, and optimizing the operational experience. Mastering the key points of customized welding table has become central for enterprises to acquire suitable equipment and enhance their competitiveness.
II. Clarifying Personalized Needs to Lay the Foundation for Customization
(A) Workpiece Characteristics Analysis
Before customization, it is essential to thoroughly sort out the characteristics of welding workpieces, including their size, weight, shape, and material. Large and heavy workpieces require workbenches with strong load-bearing capacities and stable structures. Workpieces with complex shapes necessitate workbenches equipped with special positioning and clamping devices. Different materials of workpieces also impose varying requirements on the surface treatment processes of workbenches. For example, welding aluminum workpieces requires avoiding surface scratches to prevent adverse effects on welding quality.
(B) Sorting Out Welding Process Requirements
Different welding processes have distinct requirements for workbenches. For instance, argon arc welding demands a high level of environmental cleanliness, necessitating the consideration of dust-proof and anti-static functions during customization. Laser welding places stringent demands on the stability and precision of workbenches, requiring the installation of high-precision adjustment devices and shock-absorbing structures. Clarifying commonly used welding processes and their special needs is a critical step in customizing suitable workbenches.
(C) Production Flow and Space Planning
Combining the actual production flow of enterprises, plan the functional layout and operational procedures of workbenches. Consider the paths for workpiece loading, welding, and unloading to ensure convenient and efficient operations. Meanwhile, based on the size and layout of the workshop, customize workbenches of appropriate dimensions to avoid affecting workshop passage and the operation of other equipment due to excessive size, or failing to meet production needs due to insufficient size.
III. Core Design Points to Ensure Customization Effects
(A) Structural Design Optimization
Customize the frame structure of workbenches according to the weight of workpieces and welding operational requirements. Use high-strength steel or cast iron materials and enhance the load-bearing and deformation-resistant capabilities of workbenches through reasonable mechanical designs. For scenarios requiring frequent movement of workpieces, design mobile structures equipped with reliable braking devices. For high-precision welding needs, optimize the structure to reduce the impact of vibrations on the welding process.
(B) Functional Module Customization
Integrate specific functional modules based on personalized needs. For example, customize specialized fixtures to achieve precise positioning and firm clamping of workpieces with special shapes. Add adjustable lighting systems to improve lighting conditions in the operational area. Design integrated gas and power interfaces to facilitate the connection of welding equipment and enhance operational convenience. The customization of functional modules should ensure coordinated operation among various parts without interference.
(C) Ergonomic Design
Consider the usage experience of operators and incorporate ergonomic concepts. Customize suitable workbench heights and angles to reduce fatigue from prolonged operations. Reasonably layout operational buttons, tool storage areas, etc., so that operators can easily access them, improving operational efficiency and comfort.
IV. Material and Process Selection, Determining Workbench Quality
(A) Key Points in Material Selection
Select appropriate materials based on the usage environment and load-bearing requirements of workbenches. Prioritize high-strength, corrosion-resistant steel or cast iron for the main frame to ensure structural stability. The workbench surface material should combine wear resistance, high-temperature resistance, and scratch-proof properties, such as using stainless steel or wear-resistant steel plates. For scenarios with special needs, such as anti-static workbenches, select corresponding anti-static materials.
(B) Processing Technology Control
Processing technology directly affects the quality and service life of workbenches. Pay attention to welding processes to ensure firm connections of frames without false welds or missed welds. Surface treatment processes should be refined, such as applying anti-rust coatings and wear-resistant treatments to enhance the protective performance of workbenches. For high-precision components, adopt CNC processing technology to ensure dimensional accuracy and surface finish.
V. Communication and Collaboration with Suppliers to Ensure Smooth Customization
(A) Selecting Professional Suppliers
Choose suppliers with rich customization experience and strong technical capabilities. Review suppliers' past cases to understand their design and production capabilities. Evaluate suppliers' after-sales service systems to ensure timely maintenance and technical support after equipment delivery. Establish a good communication mechanism with suppliers to facilitate timely resolution of issues during the customization process.
(B) Detailed Demand Communication
Clearly articulate customization needs to suppliers, providing detailed information on workpieces, welding process requirements, functional needs, and space constraints. Discuss design schemes with suppliers' design teams and confirm key parameters and details to avoid discrepancies between customization results and expectations due to poor communication.
(C) Production Process Follow-up
Maintain close communication with suppliers during the production process of workbenches and appropriately understand production progress and quality conditions. If necessary, arrange personnel to visit production sites to supervise key links, ensuring that the production process strictly adheres to customization requirements.
VI. Acceptance and Post-maintenance to Extend Workbench Value
(A) Strict Acceptance Standards
After workbench delivery, conduct acceptance according to customization contracts and technical requirements. Check the appearance quality to ensure no obvious defects or damages. Test various functions, such as the flexibility of adjustment devices, the firmness of clamping fixtures, and the safety and reliability of electrical systems. Measure key dimensions and performance parameters to verify compliance with customization standards. Promptly request suppliers to rectify any identified issues to ensure the equipment is qualified before being put into use.
(B) Establishing a Maintenance Mechanism
Customized welding table require regular maintenance to extend their service life. Develop a maintenance plan to regularly check structural stability, component wear, lubricate moving parts, and clean workbench surfaces and interiors of welding slag and debris. Conduct safety inspections on electrical systems and gas pipelines to promptly identify and resolve potential issues, ensuring the continuous and stable operation of workbenches.
VII. Conclusion: Customization Aids Precise Upgrades in Welding Operations
Customized welding table, through precise grasp of personalized needs, scientific design planning, high-quality material and process selection, and a comprehensive communication and maintenance process, can create tailored welding equipment for enterprises, effectively solving the problem of general-purpose equipment failing to meet special needs. Mastering customization points not only helps enterprises acquire efficient and suitable welding table but also enhances overall welding operation levels, enabling them to gain advantages in fierce market competition and driving welding production towards precise and efficient upgrades.
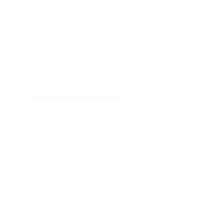
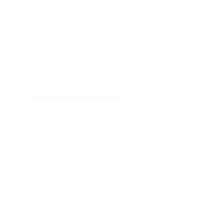
Whatapp:+86 18932785670
Tel:+86 18932785670
E-mail:project@haoranmj.com
Add:Across from Sanjing Distillery on Road 4, Botou Economic Development Zone, Cangzhou City, Hebei Province