welding table and Welding Efficiency Enhancement: Practical Methods for Equipment Optimization
Author:hxrtools Time:2025-06-16 20:26:53 Click:166
I. Introduction: The Pivotal Role of welding table in Efficiency Improvement
In contemporary industrial production, welding efficiency directly influences a company's production cycle and economic profitability. As the fundamental platform for welding operations, the performance and design of welding table are crucial determinants of welding efficiency. Optimizing welding table not only reduces time losses during operational procedures but also mitigates quality defects and rework costs arising from equipment issues. Mastering practical methods for equipment optimization has emerged as a vital pathway for enterprises to enhance welding efficiency and bolster their competitiveness.
II. Structural Optimization: Fortifying Foundations and Enhancing Operational Smoothness
(A) Strengthening Load-Bearing and Stability Design
Construct the frame of welding table using high-strength materials and enhance their load-bearing and deformation-resistant capabilities through rational mechanical designs. A stable structure minimizes positioning errors caused by workbench vibrations during the welding process, eliminating the need for repeated adjustments of workpiece positions and thus saving time. Additionally, a stable operating platform enables workers to focus more intently on welding operations, improving workflow efficiency.
(B) Optimizing Space Layout
Rationally plan the space of workbenches according to the welding process. Place commonly used tools and accessories in easily accessible locations to reduce the time workers spend searching for them. Design dedicated workpiece storage areas to streamline the loading, welding, and unloading processes, avoiding operational hindrances caused by disorganized spaces and enhancing overall work efficiency.
III. Functional Upgrades: Meeting Diverse Needs and Reducing Preparation Time
(A) Application of Flexible Adjustment Features
welding table with height and angle adjustment capabilities can swiftly adapt to the operational habits of different workers and the welding requirements of various workpieces. Workers can achieve the optimal welding state without investing significant time in adjusting their postures or workpiece angles, effectively reducing preparation time. Furthermore, the adjustable feature alleviates worker fatigue caused by prolonged maintenance of the same posture, sustaining an efficient work state.
(B) Integration of Multi-Functional Accessories
Integrating high-precision fixtures, tool slots, lighting devices, and other multi-functional accessories can significantly elevate welding efficiency. High-precision fixtures rapidly and accurately secure workpieces, reducing manual positioning time. Tool slots make commonly used tools readily accessible, preventing interruptions in operations due to tool searching. Adequate lighting devices clearly illuminate welding areas, enhancing welding precision and reducing rework caused by poor visibility.
IV. Surface Treatment Optimization: Ensuring Quality and Reducing Maintenance Costs
(A) Selecting Premium Surface Treatment Processes
Adopt anti-rust, wear-resistant, and high-temperature-resistant surface treatment processes, such as applying special anti-rust coatings and conducting wear-resistant hardening treatments. Premium surface treatments extend the service life of workbenches, minimizing the time spent on equipment maintenance and replacement due to surface damage. Meanwhile, smooth and wear-resistant surfaces resist the retention of welding slag and metal debris, facilitating cleaning, saving cleaning time, and ensuring the continuity of welding operations.
(B) Minimizing the Impact of Surface on Welding Quality
The flatness and cleanliness of the workbench surface directly affect workpiece placement and welding outcomes. Optimizing surface treatments to ensure a flat and smooth surface prevents workpiece displacement due to unstable placement, guarantees the accuracy of welding positions, reduces rework caused by welding quality issues, and thus improves overall welding efficiency.
V. Ergonomic Design: Enhancing Comfort and Sustaining Efficient Operations
(A) Rationally Designing Workbench Height and Angle
Based on ergonomic principles, design appropriate workbench heights and angles to allow workers' arms to stretch naturally during operations and maintain comfortable postures. A comfortable operational experience reduces worker fatigue, improves concentration, and extends efficient work time. Additionally, rational height and angle designs mitigate the risk of physical injuries caused by improper postures, safeguarding worker health.
(B) Optimizing Operational Interfaces and Button Layouts
Place operational buttons, control panels, etc., in easily accessible locations and adopt simple and clear designs to reduce workers' operational difficulties and learning costs. An intuitive operational interface enables workers to quickly become proficient, reducing time waste caused by unfamiliar operations and enhancing work efficiency.
VI. Daily Maintenance and Management: Ensuring Stable Equipment Operation
(A) Establishing a Regular Maintenance System
Develop a scientific maintenance plan to regularly inspect the structural stability, component wear, and functional operation status of welding table. Promptly lubricate moving parts, tighten loose connections, and clean debris from the workbench surface and interior. Good maintenance prevents equipment failures, reduces downtime caused by equipment damage, and ensures continuous and efficient welding operations.
(B) Standardizing Operational Procedures
Formulate and strictly enforce operational norms for welding table and train workers on correct operational methods. Standardized operations avoid equipment damage and efficiency reductions caused by human factors, such as overloading and improper operation of adjustment devices. Meanwhile, standardized operational procedures also contribute to improving welding quality, reducing rework, and indirectly enhancing welding efficiency.
VII. Conclusion: Scientific Optimization, Unleashing the Potential of welding table
Optimizing welding table is a systematic project for improving welding efficiency, with each link, from structural design, functional upgrades, surface treatment, to ergonomic applications and daily maintenance management, being of critical importance. Through scientific and reasonable optimization of welding table, time losses in operational processes can be effectively reduced, quality defects and rework costs can be lowered, and worker operational experiences and work efficiency can be improved. In the era of industrial production pursuing high efficiency, emphasizing the optimization of welding table is an important measure for enterprises to achieve cost reduction and efficiency enhancement, strengthen their core competitiveness, and provide strong support for the high-quality development of the welding industry.
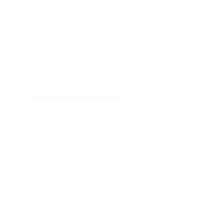
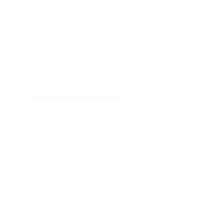
Whatapp:+86 18932785670
Tel:+86 18932785670
E-mail:project@haoranmj.com
Add:Across from Sanjing Distillery on Road 4, Botou Economic Development Zone, Cangzhou City, Hebei Province