In-Depth Analysis of Load-Bearing Capacity and Stability of welding table: Ensuring Safe and Efficient Heavy-Duty Welding Operations
Author:hxrtools Time:2025-06-18 00:14:47 Click:189
I. Introduction: Load-Bearing Capacity and Stability as Core Requirements for Heavy-Duty Welding
In heavy-duty welding operations, welding table bear large and heavy workpieces. Their load-bearing capacity and stability directly impact welding quality, production safety, and operational efficiency. If a workbench fails to withstand the weight of a workpiece or experiences shaking or deformation, it can lead to deviations in welding positions, reduced weld quality, and even serious consequences such as equipment damage and safety accidents. Therefore, gaining a deep understanding of the key factors influencing the load-bearing capacity and stability of welding table and mastering methods to ensure safe and efficient operations are of paramount importance in the field of heavy-duty welding.
II. Core Influencing Factors of Load-Bearing Capacity and Stability of welding table
(A) Importance of Material Selection
The material of a workbench determines its fundamental load-bearing capacity. High-strength steel and cast iron are common high-quality materials. Steel possesses good toughness and ductility, enabling it to withstand significant stress without easily fracturing. Cast iron, on the other hand, is renowned for its high hardness and compressive strength, making it suitable for bearing heavy loads. The thickness, density, and internal structural uniformity of the material also affect its load-bearing performance. High-quality materials not only ensure strength but also effectively reduce the risk of local deformation caused by material defects.
(B) Scientific Nature of Structural Design
Reasonable structural design is key to ensuring stability. The mechanical layout of the frame structure should conform to engineering mechanics principles. For instance, using combinations of triangular or rectangular frames can leverage the geometric stability of the structure to disperse the pressure generated by the weight of the workpiece. The number, distribution, and shape of supporting legs are also crucial. Increasing the number of supporting legs or optimizing their distribution can expand the load-bearing area and reduce pressure per unit area. Designing supporting legs in a conical or trapezoidal shape can enhance their contact stability with the ground, preventing the workbench from tilting or shaking.
(C) Reliability of Connection Processes
The connection processes between various components of a workbench directly affect its overall strength. Welding connections require full and uniform welds without any false welds or missed welds to ensure firm bonding of components. Bolted connections necessitate the use of high-strength bolts and reasonable tightening methods. Regular checks on bolt tightness are essential to prevent loosening caused by vibrations. A good connection process enables the workbench to distribute stress evenly among its components when bearing heavy loads, avoiding local stress concentration that could cause structural damage.
III. Optimization Strategies for Enhancing Load-Bearing Capacity and Stability of welding table
(A) Strengthening Material Performance and Machining Precision
When selecting materials, prioritize high-strength materials that have undergone strict quality testing and determine appropriate material specifications based on actual load-bearing requirements. Pre-treat the materials, such as by eliminating internal stresses, to improve their stability. During the machining process, ensure precision in cutting, forming, and other steps to avoid structural imbalances caused by dimensional deviations, ensuring that all components of the workbench can distribute stress evenly after assembly.
(B) Optimizing Structural Design Solutions
Tailor the structural design of the workbench according to the characteristics of heavy-duty welding operations. For oversized workpieces, design split or modular workbenches to disperse the load by increasing the number of support points. Add reinforcing ribs or beams beneath the workbench surface to enhance its resistance to bending. Additionally, consider the connection method between the workbench and the ground, using anchor bolts for fixing or adding anti-slip mats to further improve overall stability.
(C) Improving Connection and Reinforcement Measures
Enhance connection processes by adopting advanced welding techniques or high-strength connectors to increase the strength and reliability of connection areas. For key load-bearing areas, implement additional reinforcement measures, such as adding reinforcing plates or using double-bolt connections. Regularly inspect and maintain the connection areas of the workbench, promptly repairing worn or loose components to ensure that the connections remain secure.
IV. Ensuring Load-Bearing Stability through Daily Use and Maintenance
(A) Standardizing Operational Procedures
Operators must strictly adhere to the load-bearing parameters and usage instructions of the workbench, avoiding overloading. When placing heavy workpieces, distribute the load evenly to prevent excessive local pressure caused by concentrated stacking. Meanwhile, minimize severe impacts on the workbench when moving workpieces or performing welding operations to prevent vibrations from affecting structural stability.
(B) Regular Inspections and Maintenance
Establish a regular inspection system to comprehensively check the structure, connection areas, and surface wear of the workbench. Focus on inspecting critical areas such as supporting legs and frame welds for cracks, deformation, or looseness, promptly identifying and repairing potential issues. Clean and maintain the workbench surface to prevent metal corrosion from affecting material strength, extending the service life of the workbench and ensuring its load-bearing capacity and stability.
(C) Adaptive Adjustments and Improvements
With changes in welding operation requirements or the increase in the workbench's service life, make timely adaptive adjustments and improvements. For example, when the weight or size of the workpieces being carried changes, evaluate the load-bearing capacity of the existing workbench and conduct structural reinforcement or replacement if necessary. Based on actual usage feedback, optimize the detailed design of the workbench to continuously enhance its load-bearing capacity and stability performance.
V. Conclusion: Laying the Foundation for Safe and Efficient Operations
The load-bearing capacity and stability of welding table are crucial guarantees for the safe and efficient conduct of heavy-duty welding operations. By gaining a deep understanding of the core factors influencing load-bearing capacity and stability, adopting scientific and reasonable optimization strategies, and ensuring proper daily use and maintenance, the load-bearing performance and stability of workbenches can be effectively improved. In the context of the continuous development of the heavy-duty welding field, emphasizing the optimization of the load-bearing capacity and stability of workbenches not only contributes to enhancing welding quality and production efficiency but also lays a solid foundation for enterprise safety production, promoting the sustained and healthy development of the industry.
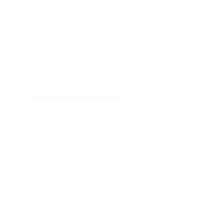
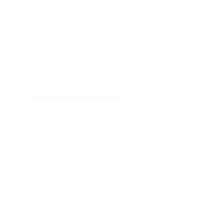
Whatapp:+86 18932785670
Tel:+86 18932785670
E-mail:project@haoranmj.com
Add:Across from Sanjing Distillery on Road 4, Botou Economic Development Zone, Cangzhou City, Hebei Province