Welding Workbench Surface Thickness: Proper Thickness Selection and Comparison of Materials
Author:hxrtools Time:2025-07-07 16:58:24 Click:178
The thickness of the welding table surface is critical in welding operations. It not only affects the stability and precision of welding but also directly impacts the longevity and cost-effectiveness of the welding table. The suitable surface thickness varies depending on the material used for the welding table. This article will discuss the appropriate surface thicknesses for common materials such as cast iron, steel plates, and stainless steel, and offer professional recommendations.
I. Cast Iron Welding Table Surface Thickness Selection
Cast iron welding table surfaces are known for their high strength, high load-bearing capacity, and excellent wear resistance. Cast iron is one of the most commonly used materials for welding tables. The common material for cast iron is HT200-250, with surface thickness typically ranging from 100mm to 300mm, depending on the size and load-bearing requirements of the welding table.
Small Welding Table
For small welding tables, such as those used for small electronic products or light mechanical parts welding, the surface thickness is generally between 100mm and 150mm. This thickness range meets the requirements for light welding tasks while controlling costs effectively. Small welding tables typically carry lighter and smaller parts, and a thickness of 100mm-150mm provides sufficient support to ensure stability during the welding process.
Large Welding Table
In large welding tables, such as those used in shipbuilding, large-scale steel structure processing, etc., the surface thickness is typically between 200mm and 300mm. Large parts are heavy, and the external forces generated during welding are also considerable. A thicker surface can bear these large weights and external forces, ensuring the platform’s stability and reliability, thus guaranteeing welding quality. For example, when welding large ship components, a welding table surface thickness above 200mm is essential.
II. Steel Plate Welding Table Surface Thickness Selection
Steel plate welding table surfaces are generally made from A3/45# steel plates, with a wide thickness range from 5mm to 50mm. Based on specific needs, steel plate welding table surfaces can be categorized into light-duty, medium-duty, and heavy-duty types.
Light-Duty Steel Plate Welding Table Surface
Light-duty steel plate welding table surfaces generally range from 5mm to 15mm in thickness, suitable for tasks such as mold flying molds, assembly, and other light operations. These tasks require relatively low load-bearing capacity from the welding table. A thickness of 5mm-15mm can meet basic support needs while maintaining the welding table's flexibility and ease of movement.
Medium-Duty Steel Plate Welding Table Surface
Medium-duty steel plate welding table surfaces are typically between 20mm and 40mm in thickness, suitable for tasks like bench work, production, and maintenance. In medium-duty tasks, the parts’ weight and size are moderate, requiring the welding table to have a certain load-bearing capacity and stability. A thickness of 20mm-40mm ensures both load-bearing capacity and cost-effectiveness.
Heavy-Duty Steel Plate Welding Table Surface
Heavy-duty steel plate welding table surfaces can be up to 50mm thick, providing high load-bearing capacity and strong impact resistance. This thickness is suitable for large parts welding and processing. In heavy-duty operations, the parts are large and carry significant impact forces. A 50mm thick surface can provide enough strength and stability to ensure that the welding table does not deform or get damaged during prolonged high-load operations.
III. Stainless Steel Welding Table Surface Thickness Selection
Stainless steel welding table surfaces are favored for their corrosion resistance, ease of cleaning, and aesthetic appeal. They can be categorized into solid and filled types.
Solid Stainless Steel Surface
Solid stainless steel surfaces typically range from 5mm to 10mm in thickness, offering high strength and wear resistance. These surfaces are suitable for welding tasks that require high hygiene and aesthetics, where load-bearing requirements are not particularly high. For example, in some food processing equipment welding, solid stainless steel surfaces can meet hygiene standards while providing adequate support.
Filled Stainless Steel Surface
Filled stainless steel surfaces are made by filling multiple layers of plate or aluminum large plates to increase thickness, typically ranging from 2cm to 4cm, and are more cost-effective. Filled stainless steel surfaces offer certain strength and stability while lowering costs, making them suitable for welding tasks that are sensitive to costs but do not have extremely high load-bearing requirements.
IV. Professional Recommendations
Choose Thickness Based on Welding Workpiece Requirements
When selecting the thickness of the welding table surface, the first consideration should be the weight, size, and welding process requirements of the workpiece. Ensure that the surface thickness can meet the needs of welding tasks to avoid deformation or damage caused by an overly thin surface, which can affect welding quality and production efficiency.
Material Selection Matters
Different materials for welding table surfaces have varying properties and applications. Cast iron welding table surfaces are suitable for high-load welding tasks; steel plate welding table surfaces offer high flexibility and cost-effectiveness, making them widely applicable; stainless steel welding table surfaces are suitable for environments that require high hygiene and aesthetics. Choose the appropriate material based on the actual working environment and needs.
Consider Economic and Practical Factors
When choosing the thickness and material for welding table surfaces, economic and practical considerations are important. Thicker surfaces have stronger load-bearing capacity but also increase costs. Thinner surfaces may not meet the needs of welding tasks. Therefore, a balance should be struck between performance and cost to reduce expenses while ensuring functionality.
Refer to Industry Experience
You can refer to the choices made by other companies in similar industries to understand the thickness and materials used in similar welding operations. This can provide insights into your own selection. Additionally, consulting with professional welding equipment suppliers can offer more specialized advice.
We specialize in the production and sale of welding tables, with extensive industry experience and a professional technical team that can provide high-quality, tailored welding table products. If you have any related needs, please feel free to contact us.
References:
·SAE International (Society of Automotive Engineers)
Research on welding table and electrical connection standards.
·IEEE (Institute of Electrical and Electronics Engineers)
In-depth study on the effects of low temperatures and material durability in welding equipment.
·ISO (International Organization for Standardization)
Welding table technical standards and quality management system requirements.
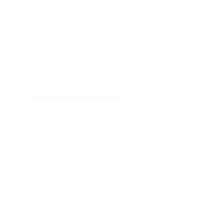
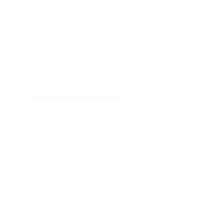
Whatapp:+86 18932785670
Tel:+86 18932785670
E-mail:project@haoranmj.com
Add:Across from Sanjing Distillery on Road 4, Botou Economic Development Zone, Cangzhou City, Hebei Province