Common causes and solutions for 3D welding platform problems
Author:hxrtools Time:2025-03-18 16:52:19 Click:173
Common causes and solutions for 3D welding platform problems:
1.3D welding platform is prone to porosity:
Because air is mixed in the molten soup;Sources of gas:during melting,in the material tube,in the mold,release agent.Improvement method:appropriate slow speed;Check whether the turning of the flow channel is smooth and whether the cross-sectional area gradually decreases;Check if the area of the airway is large enough,if it is blocked,and if it is located at the post filling area;Check if too much release agent is sprayed and if the mold temperature is too low;Use vacuum.
2.The 3D welding platform is prone to cracking:
Cracking due to contraction stress,ejection,or stress on the entire edge.Improvement method:Increase rounded corners;Check for hotspots;Change in pressurization time(cold chamber machine);Increase or shorten the mold closing time;Increase the draft angle;Increase top out sales;Check whether the mold is misaligned or deformed;Check the alloy composition.
3.The 3D welding platform is prone to peeling:
Due to poor filling mode,the molten soup overlaps;Mold deformation causes overlapping of molten soup;Inclusion of oxide layer.Improvement method:Switch to earlier;Shorten the filling time;Change the filling mode,gate position,and gate speed;Check if the mold strength is sufficient;Check if the sales mold device is in good condition;Check for the presence of an oxide layer.
4.The 3D welding platform is prone to cavitation corrosion:
Due to a sudden decrease in pressure,the gas in the molten soup suddenly expands and impacts the mold,causing damage to the mold.Improvement method:The cross-sectional area of the flow channel should not change rapidly.
5.3D welding platform is prone to cold lines:
Due to the low temperature at the front end of the molten soup,there are traces when overlapping.Improvement method:Check if the wall thickness is too thin(design or manufacturing),and fill the thinner areas directly;Check if the shape is difficult to fill;Too far away,enclosed areas(such as fins,protrusions),obstructed areas,and small rounded corners are all difficult to fill,and attention should be paid to whether there are ribs or cold spots;Shorten the filling time;Change the filling mode;Raise the mold temperature;Raise the temperature of the molten soup;Increasing the airway size may be useful;Adding a vacuum device may be useful.
Before starting work,the surface of the 3D welding platform should be cleaned.The residual gravel,burrs,etc.left after the last processing will affect the measurement accuracy.In addition,the platform may rust due to moisture or other reasons.Therefore,steel wire should be used to brush off the oil and rust parts,and the sharp edges should be trimmed.
The 3D welding platform has good micro quality,which means that the surface flatness meets the standard and the service life will be extended accordingly.In addition,improper operation and other external reasons may cause local deformation of the platform surface,which will seriously affect the measurement accuracy.Therefore,regular inspections should be carried out to solve problems in a timely manner,so as not to delay the overall work.
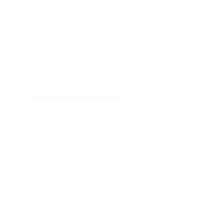
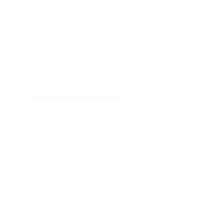
Whatapp:+86 18932785670
Tel:+86 18932785670
E-mail:project@haoranmj.com
Add:Across from Sanjing Distillery on Road 4, Botou Economic Development Zone, Cangzhou City, Hebei Province