Product Details
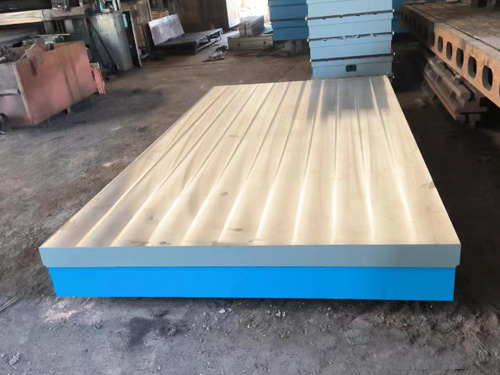
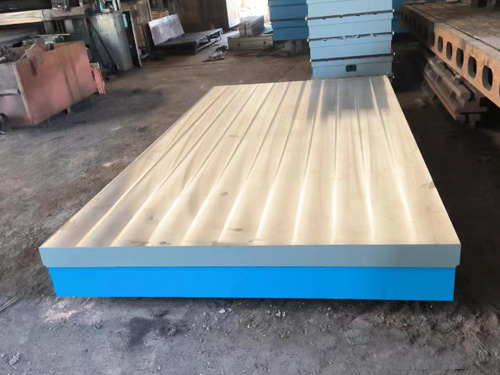
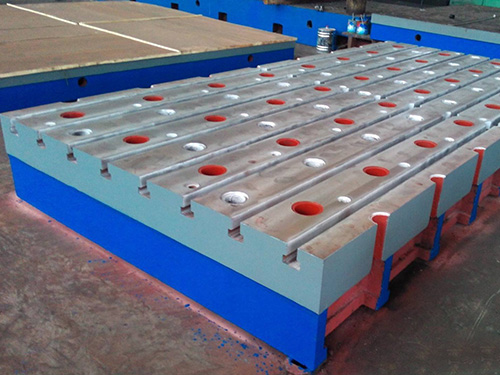
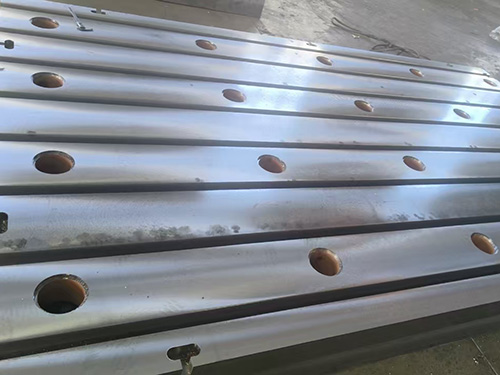
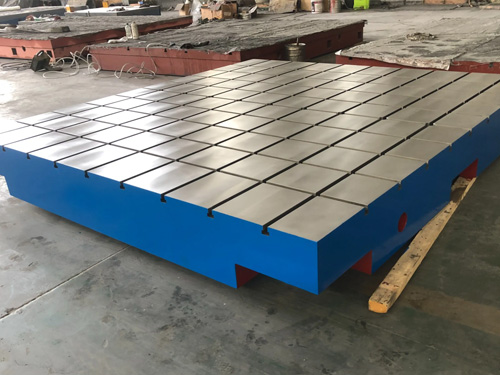
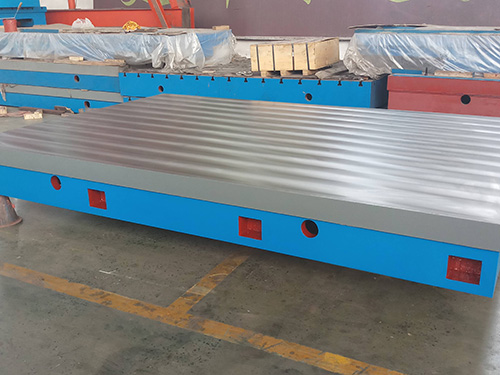
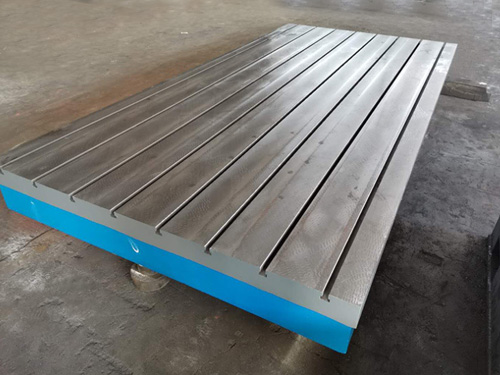
Cast Iron Test Bench
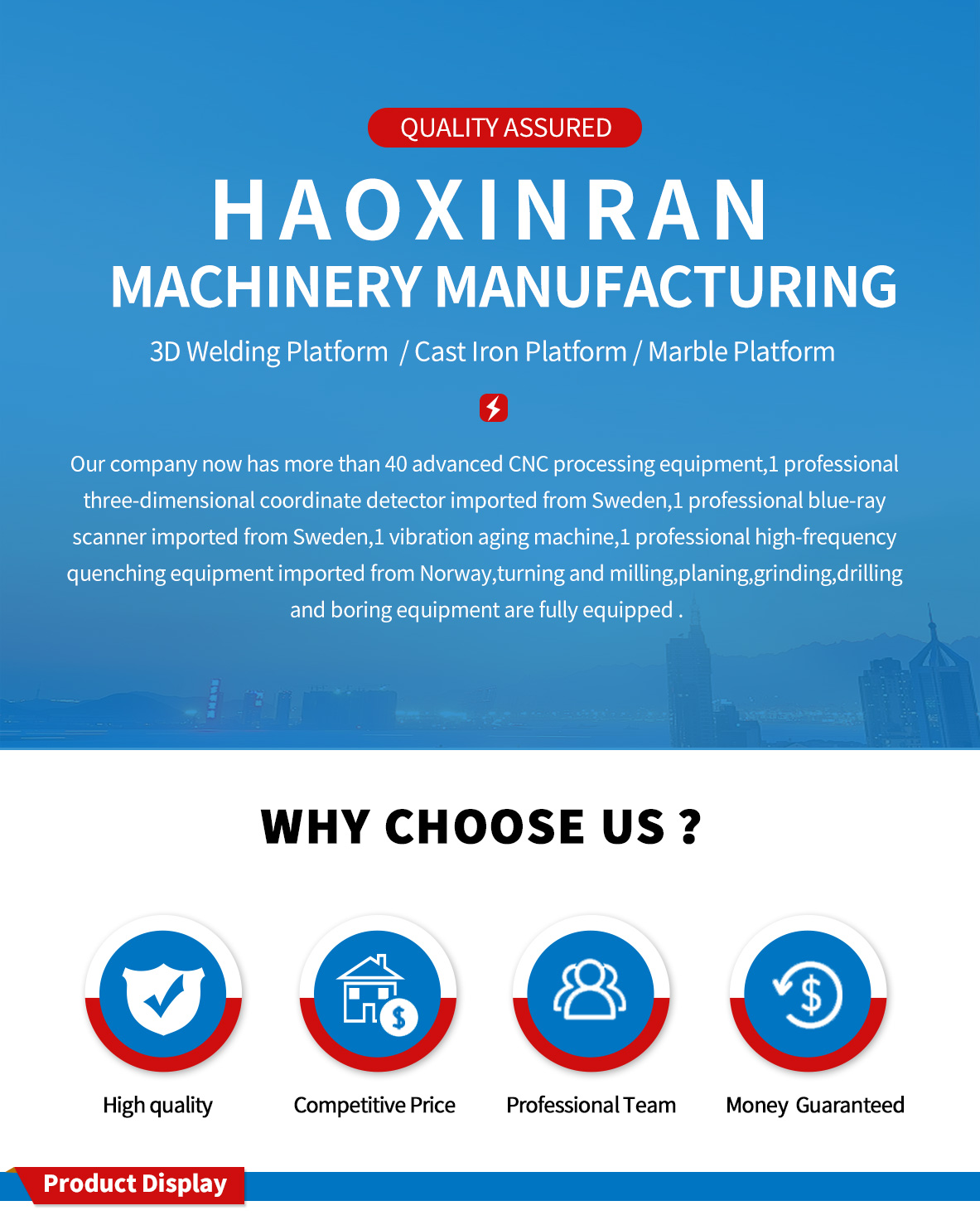
The inspection items and evaluation methods for the surface quality of cast iron test bench include the following:
(1)Roughness of cast iron test bench:the surface roughness of cast iron test bench shall be measured by contour tester,double tube microscope or interference microscope,and evaluated according to the standard.The scratch,pit and other defects on the surface of cast iron test bench rely on visual inspection.In mass production,photoelectric inspection instruments have been used to replace visual inspection instruments to inspect the surface defects of cast iron test bench.
(2)Micro defects such as cracks on cast iron test bench can be inspected by the following methods and microscope,and automatic optical scanner can be used instead of visual inspection in mass production.
1.Magnetic particle inspection method:after magnetizing the cast iron test bench,a magnetic leakage field will be generated at the crack defect.When the suspension of magnetic powder is poured,the iron powder is distributed along the magnetic force formed by the defects of the cast iron test bench.This inspection method can show the fine cracks on the surface of the cast iron test bench and the cracks under the surface.
2.Fluorescent or dye test method:the crack of cast iron test bench is revealed by the penetration of fluorescent agent or colored liquid,which is mainly used for the flaw detection of materials without magnetization.
3.Acid inspection:crack and other defects can improve the clarity after corrosion.
(3)The change of surface microhardness of cast iron test bench:measured by Vickers hardness tester.In order to measure the hardness distribution of the surface layer of the cast iron test bench,the cast iron test bench can be machined with an inclined plane of 2~3 degrees,and the thickness h of the surface layer of the cast iron test bench can be enlarged by about 25 times.
(4)Residual internal stress measurement of cast iron test bench.
1.Acid corrosion method:when the cast iron test bench has large tensile stress,cracks appear after acid retest,which can be easily used in production.
2.Layer by layer removal method:it can measure the stress distribution of the surface layer of the cast iron test bench.In this method,the surface layer is removed layer by layer by dielectric corrosion,because the deformation of parts is caused by the re balance of internal stress,and the residual internal stress can be calculated by measuring its deformation.
3.X-ray diffraction method:the change of atomic spacing can be measured by X-ray.When there is residual internal stress in the cast iron test bench,the atomic spacing in and out changes.When the spacing is larger than the normal tissue,it is tensile stress,otherwise it is compressive stress.This method can be used to measure the residual stress on the surface of cast iron test-bed.When it is necessary to measure the surface stress distribution of cast iron test bench,it shall be measured after layer by layer removal.Due to the low efficiency of this method,it is difficult to use it directly in production.X-ray diffractometer has been developed,which can determine the residual internal stress value in a few minutes.
To find out whether the datum of the scribed workpiece is flat,you can directly use the height vernier ruler to scribe on the cast iron test bench.If the datum of the scribed workpiece is the base plane,find out the base plane first,and then start from the base plane and scribe with a height vernier ruler.
Scribing alignment can be divided into blank scribing and smooth scribing:
1、When scribing on the blank,when the workpiece contacts the plane of the cast iron test bench,it is the reference plane that has been processed.There is no such alignment problem as scribing on the blank.The planning datum of processing shall be taken as the marking datum for the smooth blank marking.
1.Based on two mutually straight planes.
2.Based on a plane and a base plane.
3.Base on two mutually straight base planes.
2、The blank is basically pressed on three jacks when scribing,and the blank should be aligned first.The principle of blank alignment is as follows:
1.In order to keep the same interval between all planes,use a marking disc to level all planes,or use a square to straighten the non machined surface.
2.If several surfaces are not machined,align them with the one with a large overall area.Other surfaces that are not machined can be referred to,so that the wall thickness is as uniform as possible,and the hole is concentric with the hub or boss as much as possible.
3.If there is no plane to be machined,the cast iron test bench shall be aligned with the shape of the blank and boss of the hole to be machined.For the box with many holes,take care of the blanks and bosses of each hole,so that each hole has machining allowance and is concentric with the boss as much as possible.
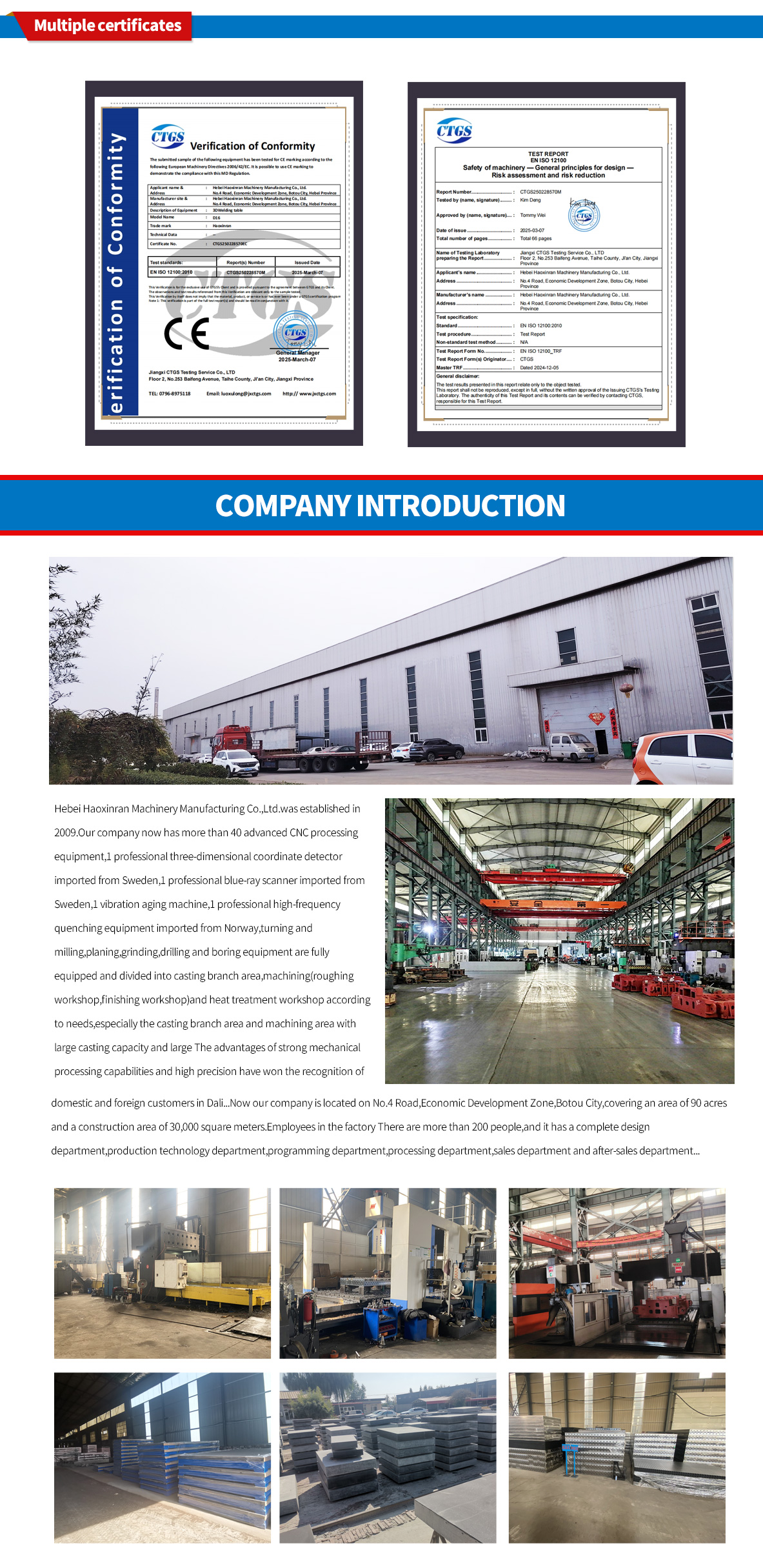
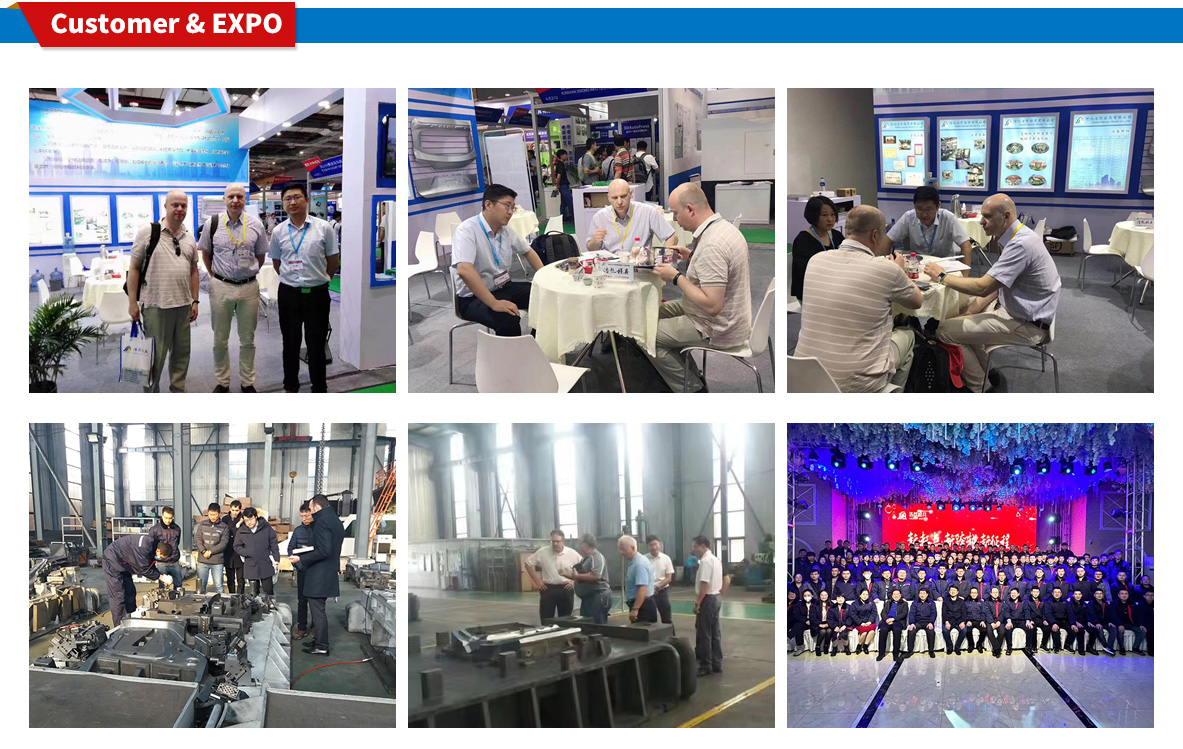
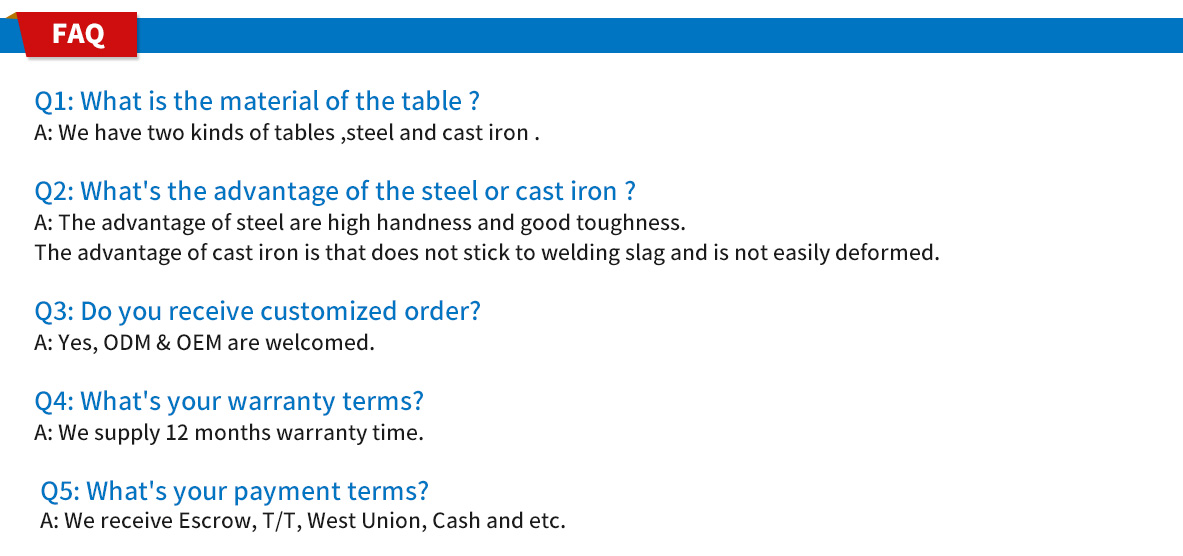
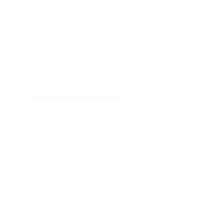
-
Beginner’s Complete Welding Table Setup Guide for 2025
2025-08-22 02:32:02
-
Welding Table Care During Extended Downtime: Essential Pre‑Use Checks
2025-08-16 05:01:04
-
Welding Table Drawer Sticking? Practical Tips for Cleaning and Lubricating Slides
2025-08-13 04:05:11
-
Welding Table Maintenance in Humid Environments: Special Anti-Corrosion Techniques
2025-08-09 09:46:55
-
How to Repair Worn Edges on a Welding Table: Correct Grinding and Weld Restoration Steps
2025-08-05 06:30:20
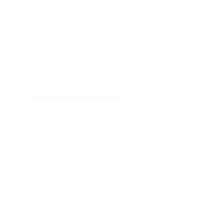
—— E-mail:project@haoranmj.com
—— Whatsapp:+86 18932785670
—— Tel:+86 18932785670
—— Add:Across from Sanjing Distillery on Road 4, Botou Economic Development Zone, Cangzhou City, Hebei Province