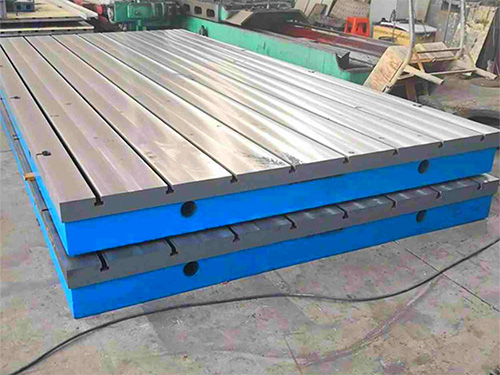
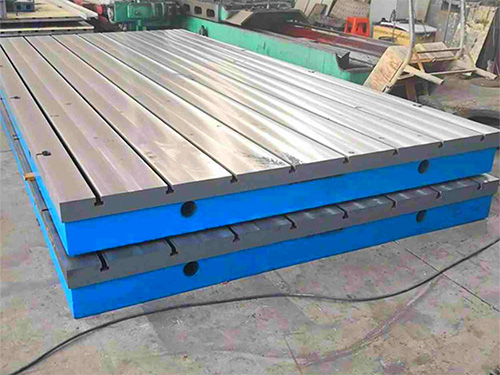
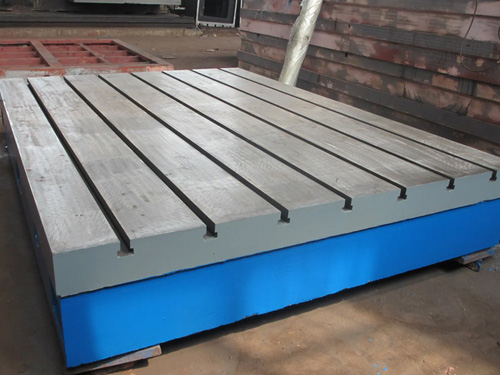
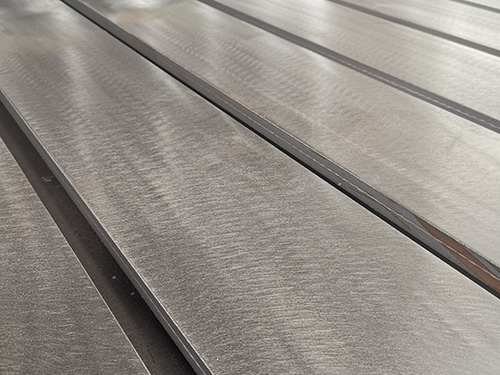
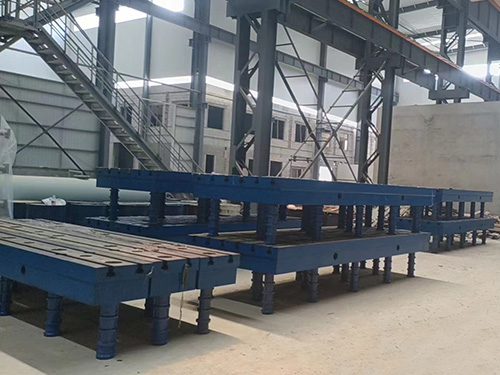
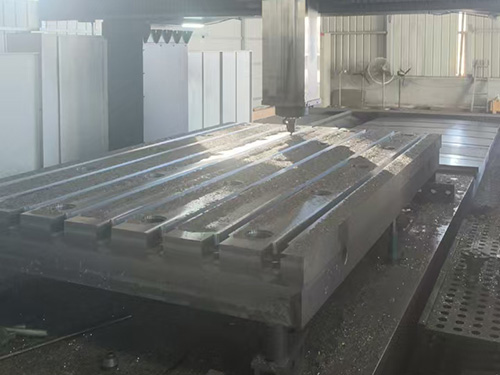
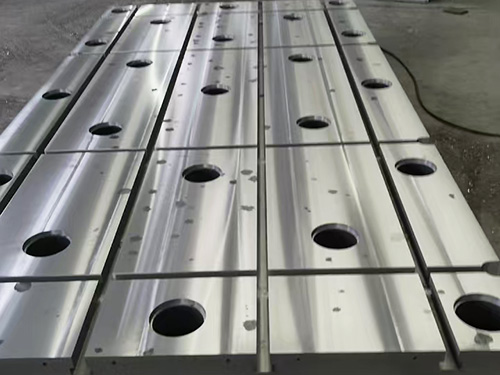
Cast Iron Inspection Platform
Specifications for Cast Iron Inspection Platform:
According to its structure,the Cast Iron Inspection Platform(cast iron flat plate)is divided into ribbed plate and box type.
According to their purposes,they are divided into testing platforms,inspection platforms,marking platforms,assembly platforms,riveting and welding platforms,welding platforms,sand pressing platforms,etc.
According to its accuracy level,it is divided into Level 1,Level 2,and Level 3 tablets,with Level 2 and above being inspection tablets and Level 3 being marking tablets.
Cast Iron Inspection Platforms are mostly box shaped structures,with T-shaped slots and circular holes on the tabletop.According to user needs,slots can be made in both horizontal and vertical directions.When processing the Cast Iron Inspection Platform,as the castings have already undergone aging treatment,the processing can be directly carried out according to the user's requirements.
The working surface of the cast iron detection platform generally has U-shaped long holes,which are mainly used to timely discharge welding slag and other debris generated during specific work,so as not to affect the cleanliness and convenience of the working surface of the cast iron detection platform.
There are various methods for the casting process of the Cast Iron Inspection Platform,as follows
1.High temperature casting
Advantages:Good fluidity,can avoid casting defects caused by bottom injection,and can produce castings with clear contours.Can avoid cracks and cold insulation defects:can avoid porosity and pinhole defects(the pouring temperature should be appropriately increased according to the casting wall thickness and structural shape,not the higher the better).
Disadvantages:prone to sand sticking defects;Easy to produce sand flushing defects;Thick and large pieces can easily cause tissue to become coarse;Thick ductile iron parts have a tendency towards shrinkage and looseness:Zengda graphite tends to float.For the production of medium and large cast iron assembly platforms,the actual pouring time and speed have a direct impact on the quality of castings.For bed castings produced using high-strength molds,a dispersed and bottom pouring method is adopted in the pouring process,supplemented by appropriately increasing the pouring speed and temperature,which can reduce the occurrence of hole type defects(air holes,slag holes,iron beans),crack type defects(hot cracking,cold cracking),surface type defects(cold shut,insufficient pouring),and tissue and performance type defects(incubation decline)in castings,improve the yield of castings,reduce waste losses,and reduce mechanical processing losses caused by internal defects in castings during the processing of cast iron assembly platforms.
2.Pour quickly
Advantages:The molten iron rises and is not easily oxidized.The baking time of the molten iron on the mold cavity is short,reducing the possibility of coating cracking and peeling,and reducing the occurrence of defects such as slag inclusion in castings;Prevent insufficient watering and cold insulation defects;Raise the pressure inside the mold cavity,forcing gas to easily escape from the mold and preventing defects such as porosity in the casting.The temperature difference between different parts of the casting is small,preventing cracks from occurring.
3.Determination of Reasonable Casting Time
The commonly used pouring time in production represents the pouring speed.For castings,a long pouring time means a slow pouring speed;conversely,it means pouring.The appropriate pouring time should be determined based on a comprehensive consideration of the quality,wall thickness,structure,technical requirements,and other factors of the bed casting.The pouring time is related to factors such as the structure,material,casting conditions,and pouring temperature of the cast iron plate.Each casting has a reasonable pouring time corresponding to it.There is no perfect calculation formula for pouring time,and it is generally determined based on various empirical formulas,charts,and casting quality.After determining the pouring time,calculate the cross-sectional area of each unit of the pouring system according to the selected section ratio.
4.Dispersed bottom pouring
Advantages:It is conducive to the smooth filling of the mold with molten metal;Reduce the oxidation of molten metal and minimize the impact force on the mold and core;Prevent sand flushing,reduce turbulence,and minimize gas entrapment;Beneficial for the discharge of cavity gas:Beneficial for slag removal:avoids excessive temperature differences in various parts,reduces casting shrinkage stress,reduces deformation for long and thin castings,and prevents crack defects from occurring.
Disadvantage:If the filling time is too long,the metal liquid will come into contact with air for a long time during the rise of the mold cavity,and the surface is prone to the formation of oxide scale(which needs to be overcome by pouring quickly);The high temperature at the lower part of the casting is not conducive to shrinkage repair(it has little effect on gray cast iron parts).
Disadvantages:Low strength sand molds are prone to sand flushing defects,which have a relatively small impact on high-strength sand molds such as resin sand.The cross-sectional area of the casting system may increase,and the casting process yield may decrease.
For the production of medium and large cast iron assembly platforms,the actual pouring time and speed have a direct impact on the quality of castings.For bed castings produced using high-strength molds,a dispersed and bottom pouring method is adopted in the pouring process,supplemented by appropriately increasing the pouring speed and temperature,which can reduce the occurrence of hole type defects(air holes,slag holes,iron beans),crack type defects(hot cracking,cold cracking),surface type defects(cold shut,insufficient pouring),and tissue and performance type defects(incubation decline)in castings,improve the yield of castings,reduce waste losses,and reduce mechanical processing losses caused by internal defects in castings during the processing of cast iron assembly platforms.
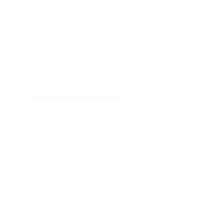
-
Welding Workbench Surface Thickness: Proper Thickness Selection and Comparison of Materials
2025-07-07 04:58:24
-
In-Depth Analysis of Load-Bearing Capacity and Stability of welding table: Ensuring Safe and Efficien
2025-06-18 12:14:47
-
welding table and Welding Efficiency Enhancement: Practical Methods for Equipment Optimization
2025-06-16 08:26:53
-
welding table and the Improvement of Welding Efficiency: Practical Methods for Equipment Optimization
2025-06-15 05:34:05
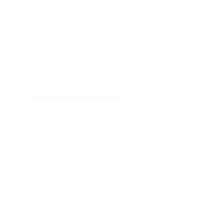
Whatapp:+86 18932785670
Tel:+86 18932785670
E-mail:project@haoranmj.com
Add:Across from Sanjing Distillery on Road 4, Botou Economic Development Zone, Cangzhou City, Hebei Province