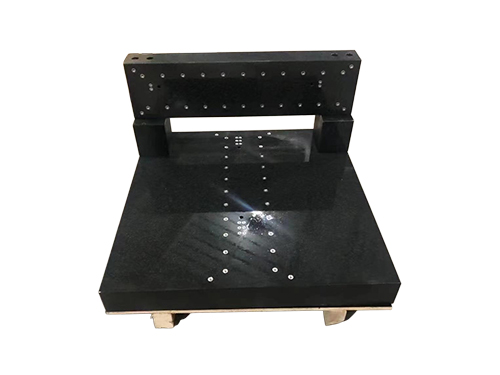
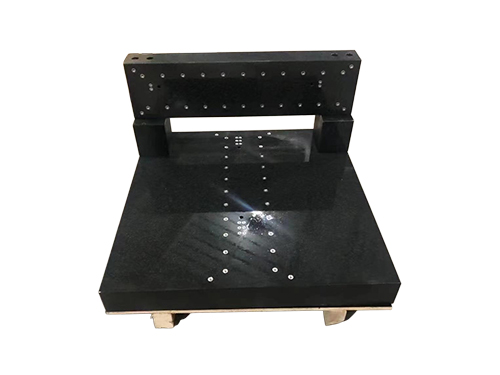
Marble components
Granite components are suitable for the working environment on site and have the characteristic of maintaining the accuracy of the product itself for a long time, which can determine the accuracy of processing and testing in the working environment and the quality of the working product. Especially for measurements with appropriate precision.
Granite components are generally used for measuring instrument workbenches, granite bed frame components, and marble components, which have the advantages of good accuracy, no deformation, high strength, and good hardness. We can process and customize according to different customer needs.
Granite bed frame components are physical measuring tools made of marble material, which have a fixed shape during use and are used to reproduce or provide one or more known quantities. For example, weights, standard batteries, color temperature lamps, resistors, measuring blocks, signal generators, and measuring instruments (single or multi value, with or without scales) are all measuring tools.
Marble measuring tools generally include: marble detection platform, marble ruler, marble square ruler, marble square ruler, marble square box, marble V-shaped block, marble comparison measuring platform, etc. Suitable for various inspection work, a reference plane for precision measurement, used as a benchmark for machine tool mechanical inspection and measurement, to check the dimensional accuracy or behavioral deviation of parts, and make lines. Marble gantry bed components are also excellent basic tools in mechanical manufacturing.
Precautions for mechanical assembly of granite components:
1. Cleaning and cleaning of good parts. The cleaning work includes removing residual casting sand, rust, chips, etc. Especially some important components, such as gantry cutting machines and inner chambers, should be coated with anti rust paint. Oil stains, rust, or attached chips on the parts can be cleaned with diesel, kerosene, or gasoline as a cleaning solution, and then dried with compressed air.
2. Lubricant is usually added to the matching surface before fitting or connecting. Especially the bearing parts in the spindle box components and the screw nut parts in the lifting mechanism.
3. The fitting dimensions of matching parts should be accurate, and the fitting dimensions should be rechecked or sampled during assembly. For example, the mating area between the journal of the spindle and the bearing, the hole and center distance between the spindle box and the bearing.
4. The assembly of the wheel requires that the axis lines of the two meshing wheels be in the same plane and parallel to each other, with normal meshing clearance and an axial displacement of 2MM.
5. The joint surface of the connection should be checked for flatness and deformation, otherwise it should be trimmed, deburred, and the joint surface should be tightly, smoothly, and not skewed.
6. The sealing element should be pressed parallel into the sealing groove, without twisting, deforming, damaging or scratching the sealing surface.
7. The assembly requirements for pulleys are that the axes of the two pulleys should be parallel, and the center of the groove should be aligned. If the offset is too large, it will cause uneven tension in the pulleys, resulting in belt slippage and accelerated wear. At the same time, the triangular belt should be selected before assembly, and the length should be consistent to prevent vibration during transmission.
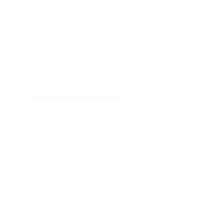
-
Welding Workbench Surface Thickness: Proper Thickness Selection and Comparison of Materials
2025-07-07 04:58:24
-
In-Depth Analysis of Load-Bearing Capacity and Stability of welding table: Ensuring Safe and Efficien
2025-06-18 12:14:47
-
welding table and Welding Efficiency Enhancement: Practical Methods for Equipment Optimization
2025-06-16 08:26:53
-
welding table and the Improvement of Welding Efficiency: Practical Methods for Equipment Optimization
2025-06-15 05:34:05
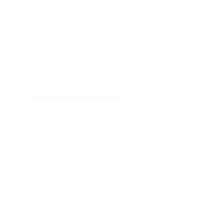
Whatapp:+86 18932785670
Tel:+86 18932785670
E-mail:project@haoranmj.com
Add:Across from Sanjing Distillery on Road 4, Botou Economic Development Zone, Cangzhou City, Hebei Province