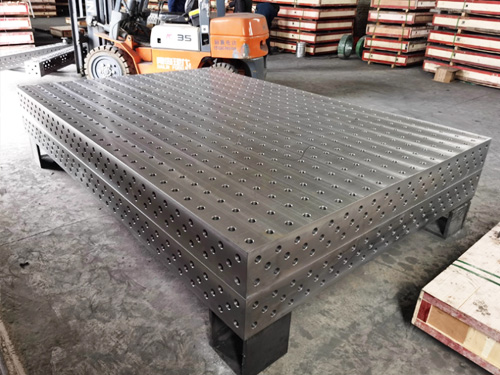
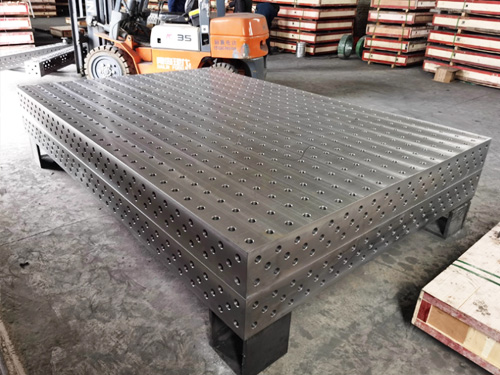
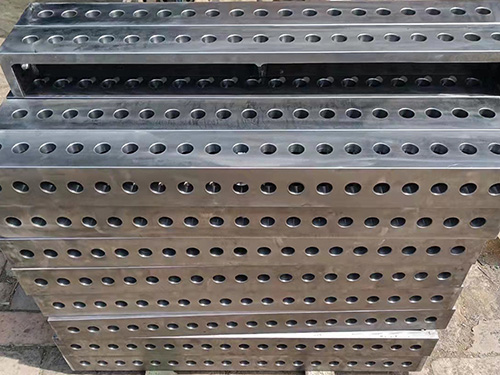
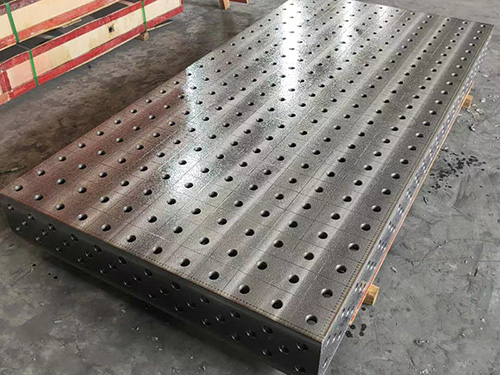
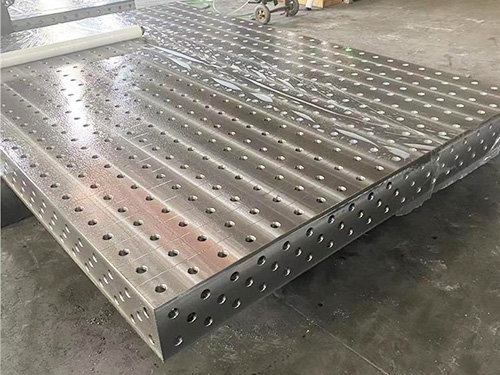
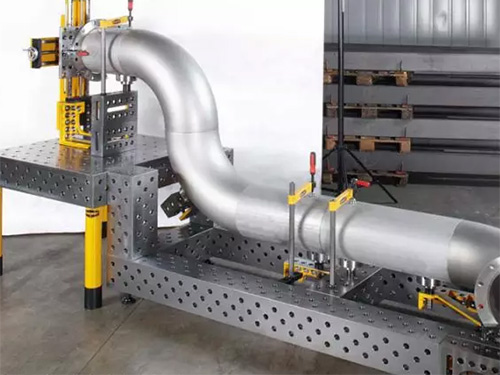
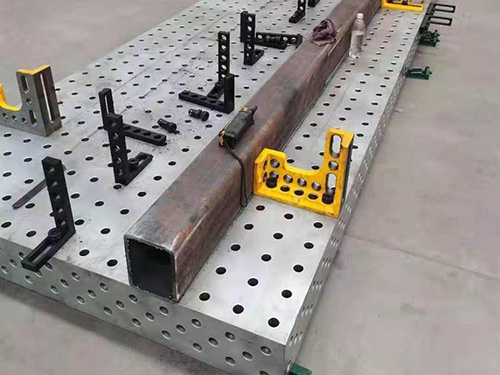
3d Casting And Welding Platform
The working surface of 3d Casting And Welding Platform adopts scraping process,and the working surface can be processed with V-shaped,T-shaped,U-shaped grooves,round holes,long holes,etc.Specification of welding platform:special specifications can be designed and produced according to user requirements.Green casting is divided into resin sand casting and cement sand casting.Now large iron castings generally use these two molding methods,both of which are lost foam casting.Generally,large batches of castings with small proportion are cast in wood mold.Resin sand casting is mainly used for machine tool castings and related welding platforms.The price is higher than that of cement sand casting.80%of the welding platforms are cast in cement sand casting,which can not only meet the requirements of the technical parameters of the welding platform,but also reduce the manufacturing cost of the welding platform.
Do you know the hardness specification of cast iron for 3D casting welding platform?Here is a detailed introduction:
1、It is used for the welding process of the workpiece.Unlike the riveting plate,there is no hole on it,and the working surface is flat or T-shaped groove.
2、The hardness of cast iron ht200-300 working face is hb170-240.After two times of manual treatment,artificial annealing 600-700 degrees and natural aging for 2-3 years,the precision of the product is stable and the performance is good.
3、Accuracy:according to the national standard metrological verification regulation,it is 0,1,2 and 3 grades respectively.
4、Specification:100*100-4000*10000,special specifications shall be made according to the drawings of the demander.
The number of auxiliary supports of 3d Casting And Welding Platform shall be determined according to the size and use of the welding platform.However,the position of the auxiliary support during the verification and use of the welding platform shall be the same as the drawing at the time of design,which determines the correct layout of the welding platform support.During use,attention should be paid to avoid excessive collision between the workpiece and the working face of the welding platform,so as to prevent damage to the working face of the welding platform;The weight of the workpiece shall not exceed the rated load of the riveting and welding platform,otherwise the work quality will be reduced,the structure of the welding platform may be damaged,and even the welding platform will be deformed and damaged,making it unusable.The accuracy grade of the welding platform is 0,1,2,3,and fine planing.The rib plate and box type working surface made of the welding platform are rectangular,square or circular.The working face adopts the scraping process,and the working face can be processed with V-shaped,T-shaped,U-shaped grooves,round holes,long holes,etc.Specification of welding platform(welding platform):(special specifications can be designed and produced according to user requirements).
The use method of three-dimensional casting welding platform,as its name implies,is to carry out welding work on the platform.It is inevitable to knock.The strength of the knock causes us to not use too thin panels.Casting method of 3D casting welding platform:the wall thickness of the welding platform casting is too thin,and casting defects such as insufficient pouring and cold shut will appear in the production of castings.This is because too thin wall thickness cannot determine that the casting alloy liquid has enough capacity to fill the mold.Generally,under the corresponding casting conditions,each casting alloy has a small wall thickness that can fill the mold,commonly known as the small wall thickness of the casting alloy.When designing castings,the design wall thickness of castings shall not be less than the small wall thickness.This small wall thickness is related to the fluidity of the casting alloy liquid and the outline size of the casting.
The characteristics of 3d Casting And Welding Platform are as follows:
1、The three-dimensional casting welding platform control system realizes the motion control of a large number of positioning points in the flexible tooling by controlling the servo motor.The function of the flexible tooling determines that in the application,it generally only cares about the position accuracy of each positioning point,but does not care about the motion trajectory accuracy.Therefore,the flexible tooling NC system generally does not need to have multi axis synchronization and interpolation functions.
2、In order to adapt to the development trend of tooling equipment integration,the flexible tooling control system should be able to adapt to a variety of bus topologies,so that it can be integrated with the CNC system of other CNC equipment.
3、The control system of v should have the ability to control a large number of actuators,especially the ability to accurately control more than 6 axes.At the same time,the tooling control system is required to be open,the number of servo shafts(motors)can be easily increased or decreased,and the increase or decrease of the number will not affect the control accuracy.
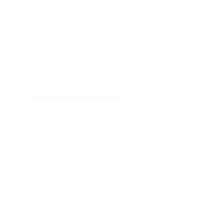
-
Welding Workbench Surface Thickness: Proper Thickness Selection and Comparison of Materials
2025-07-07 04:58:24
-
In-Depth Analysis of Load-Bearing Capacity and Stability of welding table: Ensuring Safe and Efficien
2025-06-18 12:14:47
-
welding table and Welding Efficiency Enhancement: Practical Methods for Equipment Optimization
2025-06-16 08:26:53
-
welding table and the Improvement of Welding Efficiency: Practical Methods for Equipment Optimization
2025-06-15 05:34:05
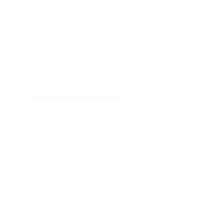
Whatapp:+86 18932785670
Tel:+86 18932785670
E-mail:project@haoranmj.com
Add:Across from Sanjing Distillery on Road 4, Botou Economic Development Zone, Cangzhou City, Hebei Province