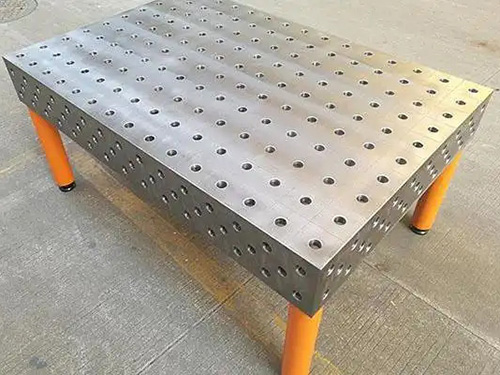
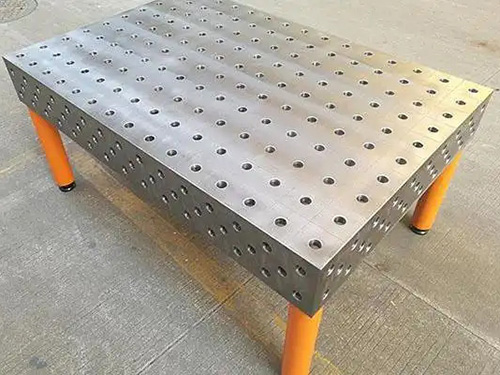
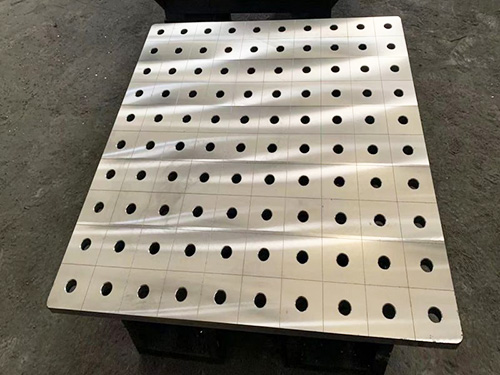
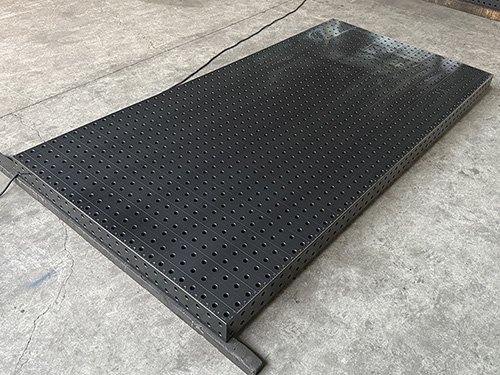
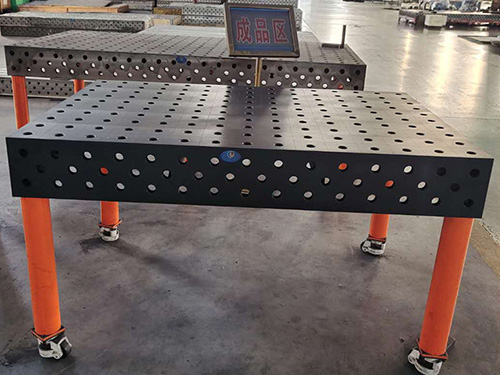
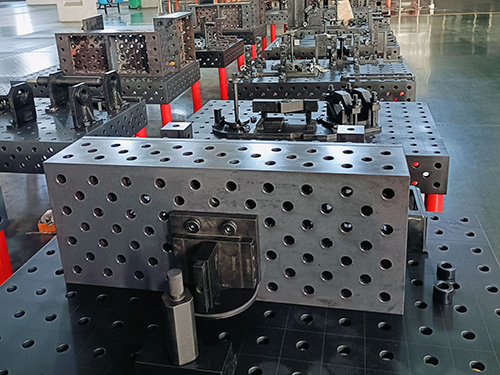
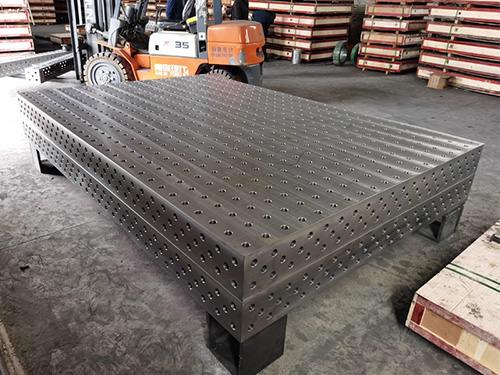
CNC welding robot
A CNC welding robot is an automated device used in welding processes that combines the precision and control of computer numerical control(CNC)technology with the functionality of a robotic arm.Here is a detailed introduction:
Components
Robotic Arm:The mechanical structure that performs the welding motion.It typically has multiple degrees of freedom,allowing it to move in various directions and positions with high accuracy.The arm is made of strong and lightweight materials to ensure smooth and precise movement while being able to handle the weight of the welding torch and other accessories.
Welding Torch:The tool attached to the robotic arm that delivers the welding energy to join the metal parts together.It can be of different types,such as MIG(Metal Inert Gas),TIG(Tungsten Inert Gas),or plasma welding torches,depending on the specific welding process and materials being used.
CNC Controller:The"brain"of the welding robot.It is a computer-based system that controls the movement of the robotic arm and the operation of the welding torch.The controller reads and executes pre-programmed instructions,which define the path,speed,and other parameters of the welding process.It also allows for real-time monitoring and adjustment of the welding operation.
Sensors:Various sensors are used to enhance the performance and accuracy of the welding robot.These include vision sensors to detect the position and shape of the workpiece,seam-tracking sensors to ensure the welding torch follows the correct path along the joint,and force sensors to monitor the contact force between the torch and the workpiece.
Working Principle
Programming:The operator first creates a program using specialized software.This program defines the welding path,speed,torch angle,and other parameters based on the specific requirements of the workpiece and the welding process.The program can be created by manually teaching the robot the desired path through a teach-pendant,or by importing a CAD/CAM model of the workpiece and generating the path automatically.
Execution:Once the program is loaded into the CNC controller,the robot begins to execute the welding operation.The controller sends signals to the motors that drive the robotic arm,causing it to move the welding torch along the pre-programmed path.At the same time,the controller also regulates the output of the welding power source to ensure the correct welding current,voltage,and wire feed speed are maintained.
Sensing and Feedback:During the welding process,the sensors continuously monitor the welding situation.If the vision sensor detects a deviation in the workpiece position or the seam-tracking sensor finds that the torch is off-track,the controller can automatically adjust the robot's movement to correct the path.The force sensor can also be used to maintain a consistent contact force between the torch and the workpiece,ensuring a high-quality weld.
Advantages
High Precision and Quality:CNC welding robots can achieve extremely high levels of accuracy in welding,resulting in consistent and high-quality welds.The precise control of the welding path and parameters reduces the occurrence of welding defects such as porosity,cracks,and uneven weld beads.This is especially important in industries where the quality and reliability of welds are critical,such as automotive,aerospace,and shipbuilding.
Increased Productivity:Robots can work continuously without interruption,24 hours a day,7 days a week,except for maintenance and programming changes.They can also weld at a faster speed than human operators,significantly increasing the production output.Additionally,the use of robots reduces the need for manual labor,which can be limited by factors such as fatigue,skill level,and work hours.
Improved Safety:Welding operations often involve exposure to high heat,sparks,fumes,and other hazardous elements.By using robots,human workers can be removed from these dangerous environments,reducing the risk of accidents and occupational health problems.This improves the overall safety of the workplace and helps companies meet safety regulations and standards.
Flexibility and Adaptability:CNC welding robots can be easily reprogrammed and adapted to different welding tasks and workpiece geometries.With the right software and tools,they can quickly switch between different welding programs,making them suitable for small-batch production as well as mass production.This flexibility allows manufacturers to respond quickly to changes in product design or production requirements.
Applications
Automotive Industry:Used for welding car bodies,chassis,and other components.The high-precision and repeatability of the robots ensure the quality and strength of the welds,which is crucial for the safety and durability of vehicles.
Aerospace Industry:In the manufacturing of aircraft structures,where the quality and reliability of welds are of utmost importance.Robots are used to weld complex and high-strength materials with strict quality control.
Shipbuilding Industry:For welding the large-scale structures of ships,such as hulls and decks.The ability of robots to work in harsh environments and handle heavy-duty welding tasks makes them well-suited for this industry.
Metal Fabrication:In general metal fabrication shops,robots are used to weld various metal components,including pipes,beams,and machinery parts.They can handle a wide range of materials and thicknesses,improving the efficiency and quality of the fabrication process.
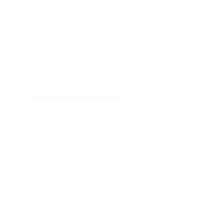
-
Welding Workbench Surface Thickness: Proper Thickness Selection and Comparison of Materials
2025-07-07 04:58:24
-
In-Depth Analysis of Load-Bearing Capacity and Stability of welding table: Ensuring Safe and Efficien
2025-06-18 12:14:47
-
welding table and Welding Efficiency Enhancement: Practical Methods for Equipment Optimization
2025-06-16 08:26:53
-
welding table and the Improvement of Welding Efficiency: Practical Methods for Equipment Optimization
2025-06-15 05:34:05
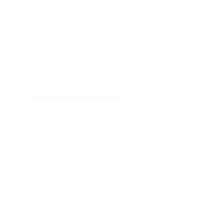
Whatapp:+86 18932785670
Tel:+86 18932785670
E-mail:project@haoranmj.com
Add:Across from Sanjing Distillery on Road 4, Botou Economic Development Zone, Cangzhou City, Hebei Province