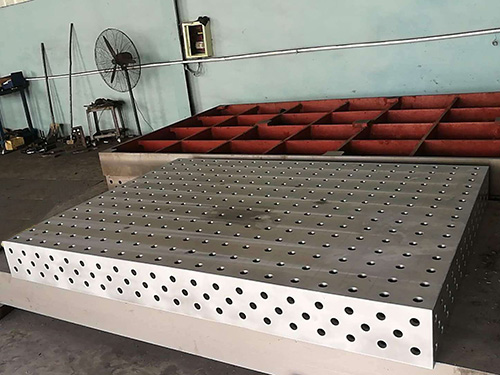
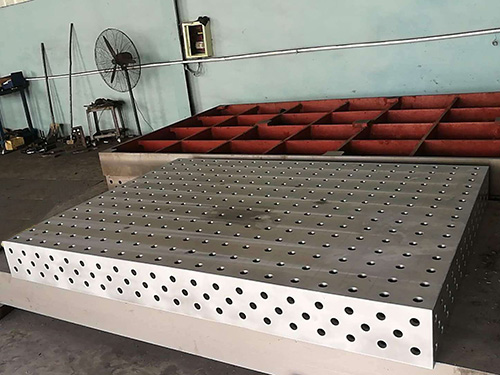
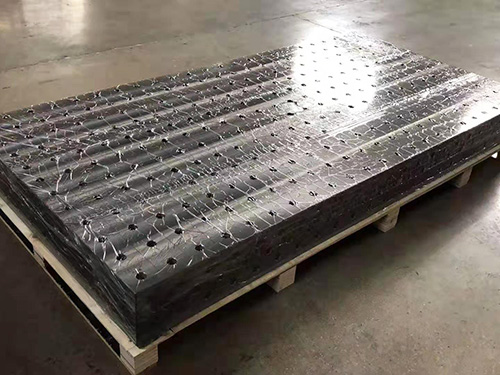
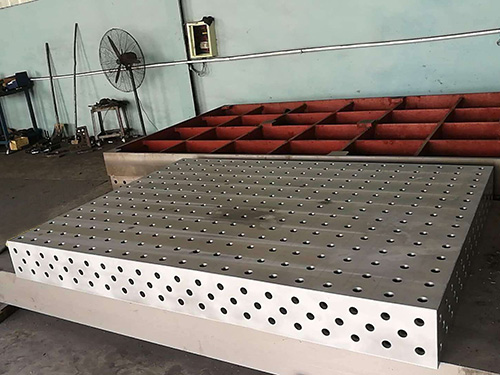
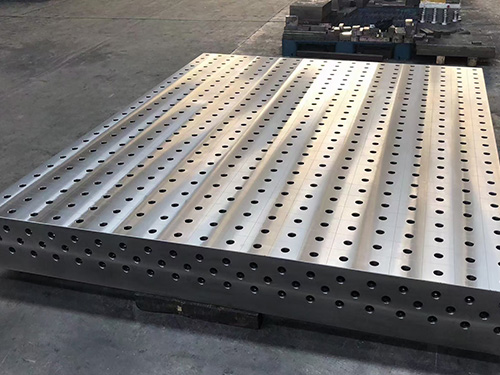
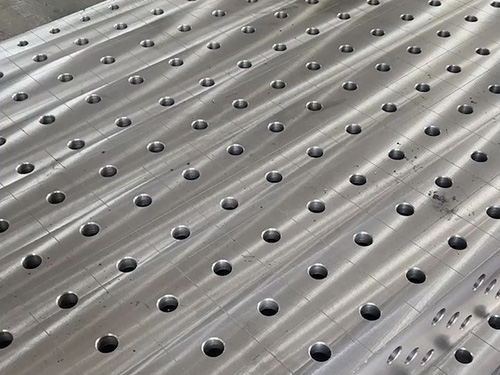
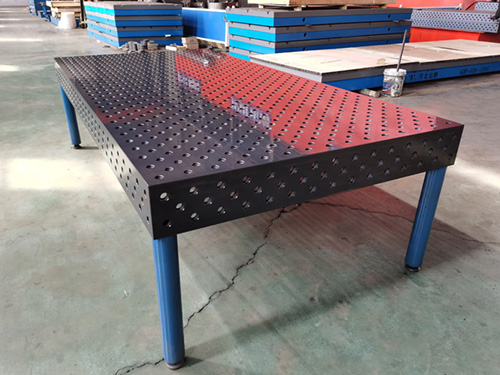
Laser Cutting Welding Table
The Laser Cutting Welding Table is an advanced equipment that integrates laser cutting and welding functions, widely used in modern manufacturing for high-precision processing of metals or other materials. Here is a detailed introduction to it:
Function integration: The biggest feature of the laser cutting and welding workbench is to integrate the two important processing technologies of laser cutting and laser welding on the same workbench. By switching between different working modes and parameter settings, it can quickly switch between cutting and welding functions, achieving one-stop machining of workpieces. For example, using laser cutting function to cut the sheet metal into specific shapes and sizes according to design requirements, and then directly switching to welding mode on the same workbench, these parts are welded and assembled into a complete product, greatly improving production efficiency and reducing errors and damages that may occur when workpieces are transferred between different equipment.
High precision machining: Laser technology itself has the characteristic of high precision, which enables the laser cutting and welding worktable to achieve extremely high precision during the machining process. In terms of cutting, laser beams can focus on very small light spots, narrow cutting seams, and can cut complex geometric shapes and fine patterns with cutting accuracy up to millimeter or even sub millimeter levels. During welding, the laser beam can accurately act on the welding area to achieve high-quality welding joints. The welding depth and width can be precisely controlled, and the welding quality is stable with minimal deformation. It is particularly suitable for precision parts with high precision requirements, such as electronic components, medical equipment components, etc.
Workbench structure: In order to meet the requirements of laser cutting and welding work, the workbench structure is usually designed to be sturdy and stable. The countertop is generally made of high-strength and high-precision materials, such as high-quality steel or marble, which have good flatness and rigidity, can withstand the impact force and thermal stress during the processing, and ensure the positional accuracy of the workpiece during the processing. At the same time, the motion system of the workbench is also carefully designed, usually using high-precision linear guides, ball screws, servo motors and other components, which can achieve fast and accurate movement and positioning, meeting the requirements of laser processing for motion accuracy.
Automation control system: Equipped with advanced automation control system, operators can set and adjust various parameters of the workbench through computer software, such as laser power, cutting speed, welding time, etc. The control system also has programming functions, which can write processing programs based on the design drawings of the workpiece to achieve automated processing. In addition, some high-end laser cutting and welding workbenches are equipped with visual recognition systems that can automatically locate and detect workpieces, further improving the accuracy and efficiency of processing.
Safety protection: Due to the high energy and potential danger of lasers, laser cutting and welding workbenches are usually equipped with comprehensive safety protection devices. For example, there are protective fences or covers around the workbench to prevent laser leakage from causing harm to operators; The laser processing area is equipped with warning signs and safety interlock devices. When the protective door is opened, the laser system will automatically stop working to ensure the safety of operators.
Application areas: Widely used in multiple industries, such as the electronic manufacturing industry for cutting and soldering circuit boards, electronic components, etc; Used in the automotive manufacturing industry for the processing and assembly of body parts; The aerospace industry is used to manufacture high-precision aviation components; The jewelry industry is used for cutting and welding precious metals. It plays an important role in promoting the development of manufacturing towards high precision, high efficiency, and automation.
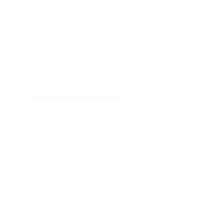
-
Key Points for Selecting Granite Surface Plates: Matching Dimensions, Thickness, and Machining Proces
2025-05-20 02:29:03
-
Classification and detection of flatness of cast iron flat platform
2025-03-26 09:48:15
-
Daily maintenance of cast iron platform
2025-03-26 09:46:59
-
How to solve the shrinkage and loosening defects of cast iron platforms?
2025-03-18 04:54:34
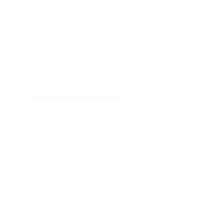
Whatapp:+86 18932785670
Tel:+86 18932785670
E-mail:project@haoranmj.com
Add:Across from Sanjing Distillery on Road 4, Botou Economic Development Zone, Cangzhou City, Hebei Province