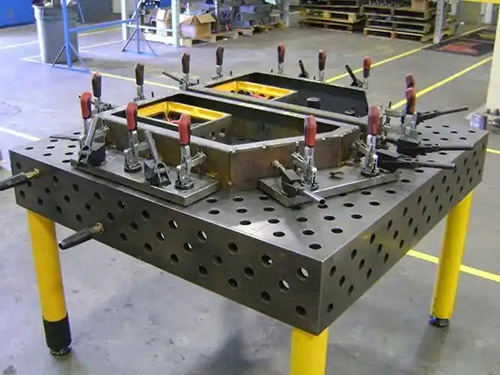
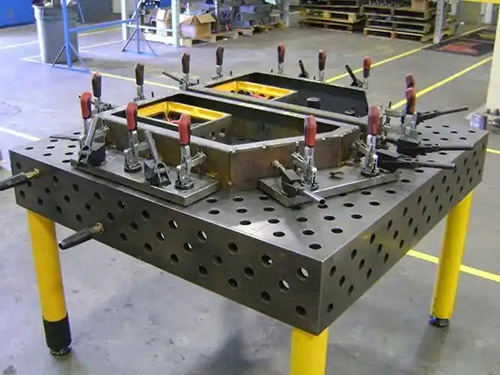
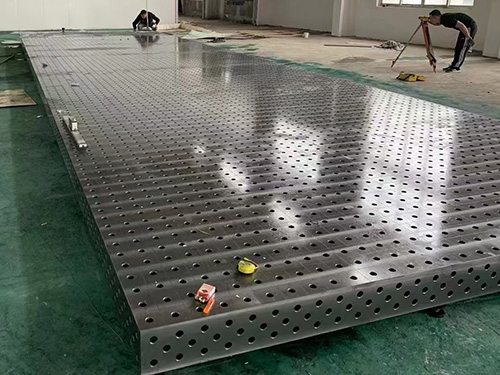
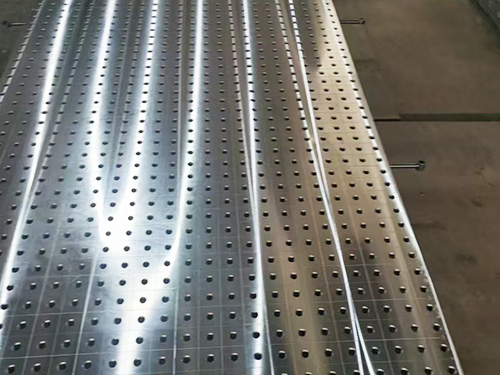
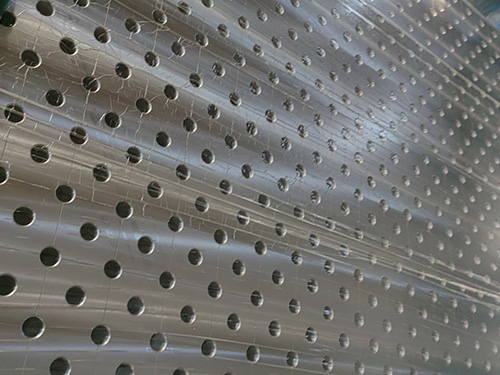
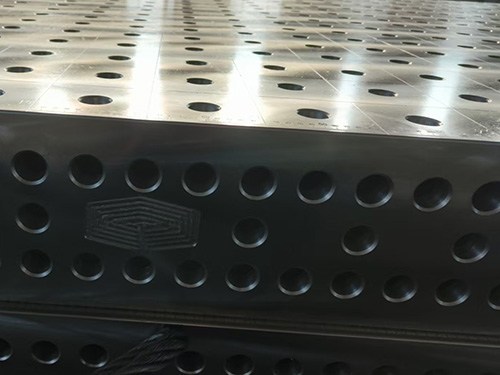
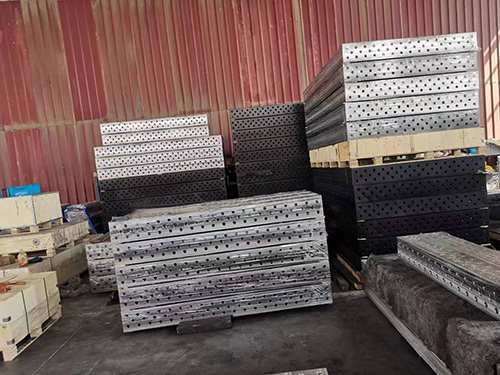
Smart Welding Table
A Smart Welding Table is an advanced piece of equipment that combines traditional welding table functionality with intelligent features to enhance the efficiency,precision,and safety of welding operations.Here is a detailed introduction:
1.Key Features
Automated Positioning and Adjustment:Smart welding tables are equipped with advanced motion control systems,such as servo motors and linear actuators.These systems can automatically position workpieces with high precision.For example,they can adjust the height,angle,and orientation of the work surface or the workpiece fixtures according to pre-programmed instructions.This eliminates the need for manual and often time-consuming adjustments,ensuring consistent and accurate welding positions every time.
Integrated Sensors:A variety of sensors are integrated into the table.These include temperature sensors to monitor the heat generated during welding,strain sensors to detect any abnormal stresses on the table or the workpiece,and position sensors to keep track of the exact location of components.For instance,temperature sensors can help prevent overheating of the workpiece or the table surface,while strain sensors can alert operators to potential structural issues before they cause damage.
Digital Control and Connectivity:Smart welding tables are typically controlled via a digital interface,such as a touchscreen or a computer.Operators can easily input welding parameters,such as welding speed,current,and voltage,and the table will adjust accordingly.Moreover,these tables often have connectivity features,such as Wi-Fi or Ethernet,allowing them to be connected to a factory network.This enables remote monitoring and control,as well as data collection and analysis for process optimization.
Programmable Welding Sequences:Users can program complex welding sequences into the table's control system.This means that for repetitive welding tasks,the table can automatically perform a series of operations in the correct order,reducing the potential for human error.For example,it can move the workpiece to different positions for multiple welds,change welding parameters as required,and even pause for inspection or other operations.
Augmented Reality(AR)and Virtual Reality(VR)Integration:Some advanced smart welding tables incorporate AR or VR technologies.AR can be used to overlay virtual instructions,such as welding paths or safety warnings,directly onto the physical workpiece,guiding the operator during the welding process.VR can be used for training purposes,allowing operators to practice welding in a simulated environment before working on actual components.
2.Construction and Materials
Materials:
High-strength Steel:The frame and structure of the smart welding table are usually made of high-strength steel to ensure stability and durability.This material can withstand the mechanical stresses and vibrations generated during welding operations.
Composite Materials:In some cases,composite materials may be used for certain components to reduce weight while maintaining strength.For example,the work surface might be made of a composite material that has good heat resistance and wear resistance.
Electrical and Electronic Components:The table is equipped with a variety of electrical and electronic components,including sensors,controllers,and actuators.These components are carefully selected for their reliability and compatibility with the overall system.
Construction:The construction of a smart welding table is more complex than a traditional welding table due to the integration of electronic and mechanical components.The electrical and electronic systems are carefully routed and protected to prevent interference and damage.The mechanical components,such as the motion control systems,are precisely assembled and calibrated to ensure smooth and accurate operation.
3.Applications
Aerospace Manufacturing:In the aerospace industry,where precision and quality are of utmost importance,smart welding tables are used for welding critical components such as aircraft engine parts and structural elements.The automated positioning and precise control features help ensure the high quality and reliability of the welds,which are essential for the safety of aircraft.
Automotive Industry:Smart welding tables are used in automotive manufacturing for welding body panels,chassis components,and engine parts.The programmable welding sequences and automated adjustments improve production efficiency and reduce the number of defective parts.Additionally,the data collection and analysis capabilities of these tables can be used to optimize the welding process and improve overall production quality.
Medical Device Manufacturing:For the production of medical devices,which require extremely high precision and cleanliness,smart welding tables provide a controlled environment for welding operations.The integrated sensors and digital control features help ensure that the welds are of the highest quality,meeting the strict regulatory requirements of the medical industry.
High-tech Electronics:In the electronics industry,where small and delicate components need to be welded,smart welding tables offer the precision and control needed.The AR and VR integration can be particularly useful for guiding operators in the welding of tiny components,reducing the risk of errors and improving the yield of the production process.
4.Maintenance and Care
Software and Firmware Updates:Regularly update the software and firmware of the smart welding table to ensure that it has the latest features and security patches.This helps to maintain the performance and reliability of the table's control system.
Sensor Calibration:Periodically calibrate the sensors to ensure accurate readings.Incorrect sensor readings can lead to improper operation of the table or poor quality welds.Follow the manufacturer's instructions for calibration procedures.
Electrical and Mechanical Inspection:Conduct regular inspections of the electrical and mechanical components of the table.Check for loose connections,damaged wires,or worn-out mechanical parts.Replace any components that are found to be defective to prevent breakdowns during operation.
Cleaning and Lubrication:Keep the table clean,especially the work surface and the moving parts.Remove any welding debris or contaminants that may accumulate.Lubricate the moving parts as recommended by the manufacturer to ensure smooth operation and reduce wear.
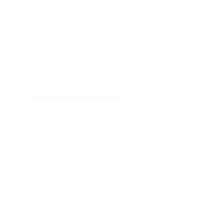
-
Welding Workbench Surface Thickness: Proper Thickness Selection and Comparison of Materials
2025-07-07 04:58:24
-
In-Depth Analysis of Load-Bearing Capacity and Stability of welding table: Ensuring Safe and Efficien
2025-06-18 12:14:47
-
welding table and Welding Efficiency Enhancement: Practical Methods for Equipment Optimization
2025-06-16 08:26:53
-
welding table and the Improvement of Welding Efficiency: Practical Methods for Equipment Optimization
2025-06-15 05:34:05
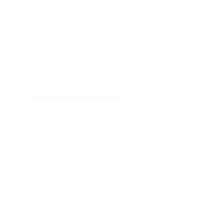
Whatapp:+86 18932785670
Tel:+86 18932785670
E-mail:project@haoranmj.com
Add:Across from Sanjing Distillery on Road 4, Botou Economic Development Zone, Cangzhou City, Hebei Province