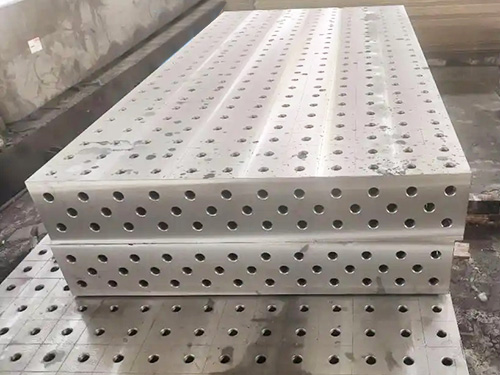
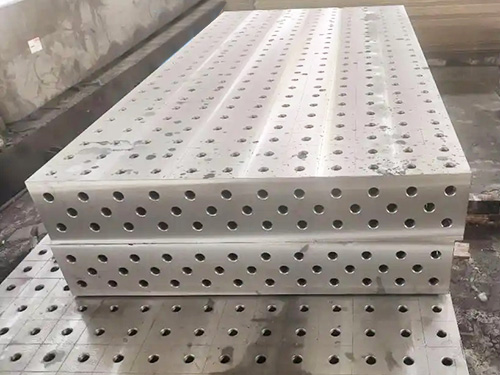
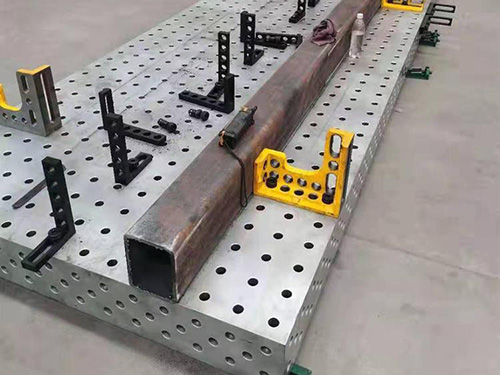
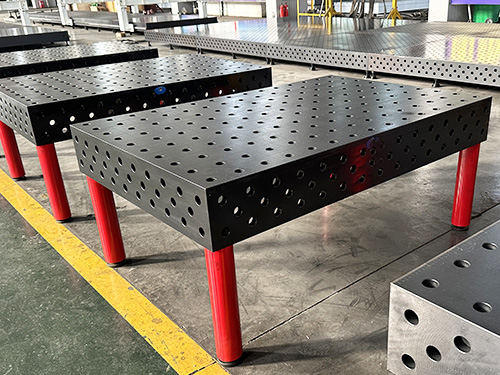
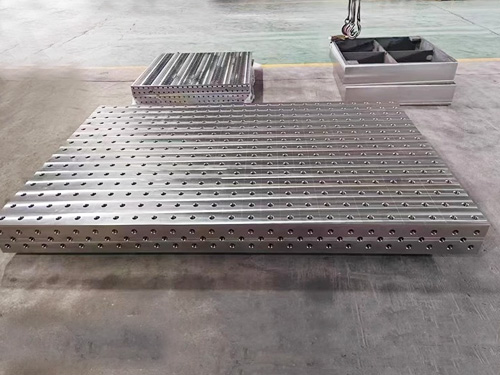
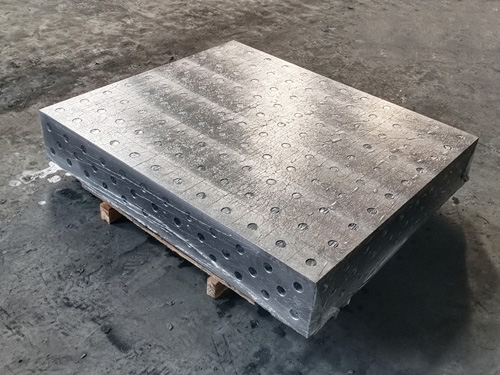
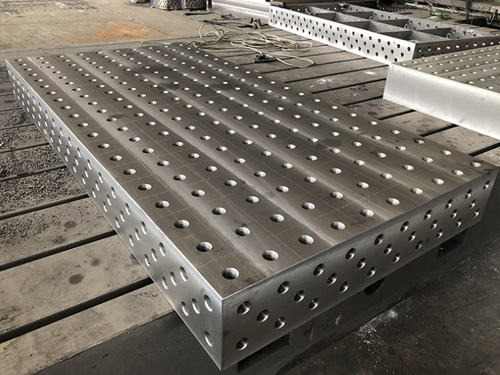
Welding workbench clamp
A welding workbench clamp is an essential tool used in welding operations to secure workpieces firmly in place. Here is a detailed introduction:
Types of Welding Workbench Clamps
Parallel Jaw Clamps: These are the most common type. They have two parallel jaws that can be adjusted to grip workpieces of different sizes. The jaws provide a uniform clamping force across the workpiece, ensuring it remains stable during welding. They are suitable for a wide range of applications, from small-scale projects to large industrial welding tasks.
C-Clamps: Named for their C - shaped frame, these clamps are versatile and can be used to clamp workpieces at various angles. They are often used when access to the workpiece from the side is required. C - clamps come in different sizes and clamping capacities, allowing for flexibility in different welding scenarios.
Bar Clamps: These clamps consist of a long bar with adjustable jaws at each end. They are ideal for clamping long or rectangular workpieces, providing a strong and even clamping force along the length of the workpiece. Bar clamps are commonly used in woodworking and metalworking, including welding, when dealing with larger and more extended materials.
Toggle Clamps: Toggle clamps use a lever - action mechanism to quickly clamp and release workpieces. They offer a fast and efficient way to secure workpieces, especially in situations where frequent clamping and unclamping are required. Toggle clamps are often used in production - line welding processes or in workshops where time - saving is a priority.
Features and Benefits
Strong Clamping Force: Welding workbench clamps are designed to provide a strong and reliable clamping force to hold workpieces firmly in place. This is crucial during welding as it prevents the workpiece from moving or shifting due to the heat and force generated during the welding process, ensuring accurate and high - quality welds.
Adjustability: Most welding clamps are adjustable, allowing for easy adaptation to different workpiece sizes and shapes. This adjustability ensures a proper fit and secure clamping, regardless of the specific dimensions of the material being welded. Some clamps may have fine - tuning mechanisms to achieve precise clamping positions.
Durability: Made from high - quality materials such as hardened steel or cast iron, welding workbench clamps are built to withstand the harsh conditions of a welding environment. They are resistant to heat, wear, and corrosion, ensuring a long service life even with frequent use. The robust construction of the clamps also enables them to handle heavy - duty welding tasks without losing their clamping effectiveness.
Versatility: Welding clamps can be used in various welding techniques, including MIG, TIG, and stick welding. They are suitable for different types of workpieces, such as metal sheets, pipes, and structural components. Additionally, they can be used in combination with other welding accessories and fixtures to create a customized welding setup for specific projects.
How to Use Welding Workbench Clamps
Select the appropriate clamp: Based on the size, shape, and material of the workpiece, choose the most suitable type of clamp. Consider factors such as the required clamping force, access to the welding area, and the need for adjustability.
Position the workpiece: Place the workpiece on the welding workbench in the desired position for welding. Ensure that it is properly aligned and centered before clamping.
Attach the clamp: Position the clamp on the workpiece, making sure that the jaws grip the material firmly and evenly. Tighten the clamp using the appropriate mechanism, such as a screw - type adjustment or a lever - action handle, until the workpiece is held securely in place.
Check the clamping force: Before starting the welding process, double - check that the clamp is providing sufficient clamping force to prevent the workpiece from moving. Make any necessary adjustments to ensure a stable and secure clamping.
Remove the clamp after welding: Once the welding is complete and the workpiece has cooled down, carefully release the clamp and remove it from the workpiece. Inspect the clamp for any signs of damage or wear and clean it if necessary before storing it for future use.
Maintenance and Care
Regular cleaning: After each use, clean the clamps to remove any welding spatter, dirt, or debris that may have accumulated on the jaws or other parts. Use a wire brush or a clean cloth to wipe away the contaminants. This helps to maintain the clamping performance and prevent damage to the workpiece surface.
Lubrication: Apply a suitable lubricant to the moving parts of the clamp, such as the screw threads and the pivot points. This ensures smooth operation and reduces friction, making it easier to adjust the clamp and prolonging its lifespan. Use a lubricant that is resistant to heat and chemicals commonly found in a welding environment.
Inspection for damage: Regularly inspect the clamps for any signs of damage, such as cracks, bent jaws, or worn - out threads. If any damage is detected, repair or replace the clamp immediately to avoid any potential safety hazards or compromised welding quality.
Proper storage: Store the welding workbench clamps in a dry and organized manner when not in use. Keep them away from moisture, which can cause rusting, and store them in a toolbox or a designated storage area to prevent loss or damage.
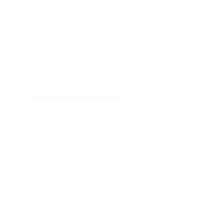
-
Welding Workbench Surface Thickness: Proper Thickness Selection and Comparison of Materials
2025-07-07 04:58:24
-
In-Depth Analysis of Load-Bearing Capacity and Stability of welding table: Ensuring Safe and Efficien
2025-06-18 12:14:47
-
welding table and Welding Efficiency Enhancement: Practical Methods for Equipment Optimization
2025-06-16 08:26:53
-
welding table and the Improvement of Welding Efficiency: Practical Methods for Equipment Optimization
2025-06-15 05:34:05
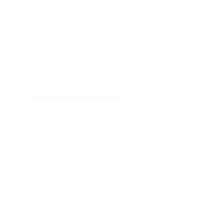
Whatapp:+86 18932785670
Tel:+86 18932785670
E-mail:project@haoranmj.com
Add:Across from Sanjing Distillery on Road 4, Botou Economic Development Zone, Cangzhou City, Hebei Province