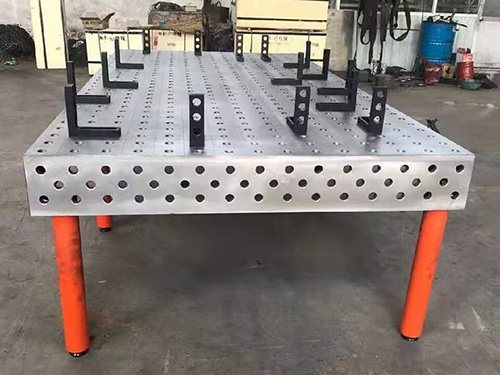
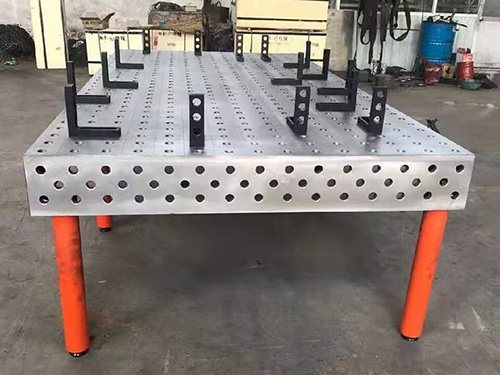
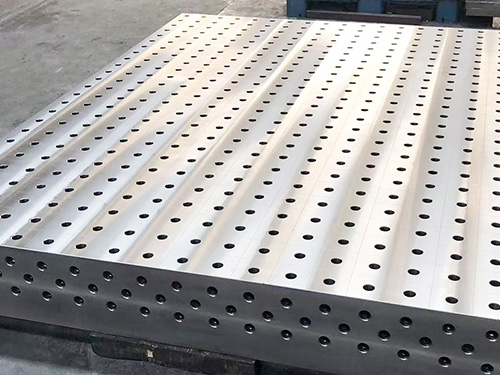
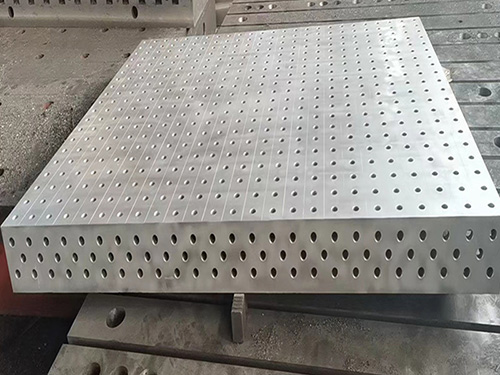
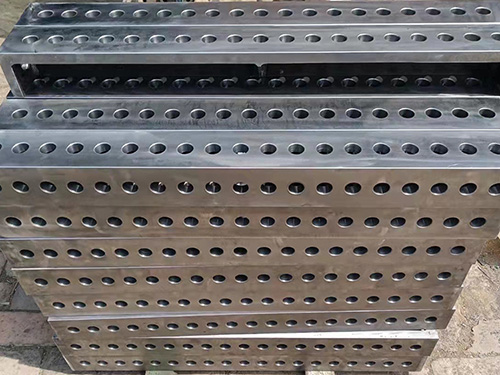
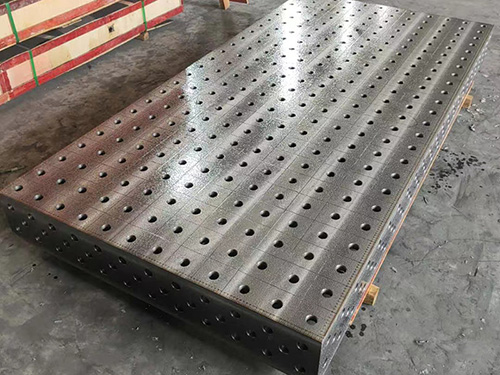
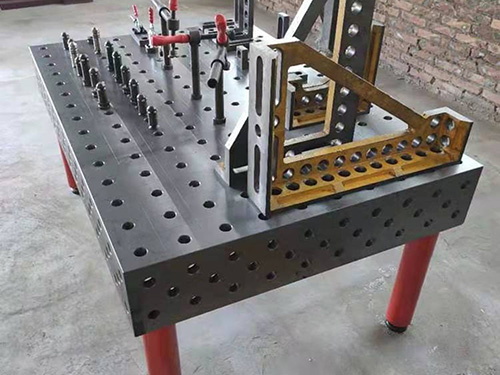
Work Bench Tool Cabinet Workshop
Introduction to the 3D Platform Used in the 3D Workbench Tool Cabinet Workshop:
The furnace material of a three-dimensional flexible welding platform is generally composed of iron,scrap steel,recycled materials,and ferroalloys.Adding scrap steel to reduce the carbon content of molten iron can improve the mechanical properties of gray cast iron.When producing different grades of gray cast iron,adding different proportions of scrap steel is used as a control indicator to determine the material properties.In recent years,due to the developed industry and abundant supply of scrap steel,which is much cheaper than iron,synthetic cast iron and its smelting methods have been developed that only use scrap steel and recycled materials instead of iron,and adjust the carbon content through carbonization methods.Synthetic cast iron not only reduces costs,but also achieves good mechanical properties with the same chemical composition.The production of synthetic cast iron requires melting equipment that can overheat the temperature of the molten iron to over 1500℃.Priority is given to sand casting.According to statistics,in China,60%to 70%of all castings are produced using sand molds,and about 70%of them are produced using clay sand molds.The main reason is that sand casting has a lower cost,simpler production process,and shorter production cycle compared to other casting methods.So castings such as engine cylinder blocks,cylinder heads,crankshafts,etc.for cars are produced using clay green sand technology.When the wet mold cannot meet the requirements,consider using clay sand surface dry sand mold,dry sand mold or other sand molds.The weight of castings cast with clay green sand can range from a few kilograms to tens of kilograms,while castings produced with clay dry molds can weigh up to tens of tons.
How to reduce casting defects in 3D flexible welding platforms?
1、The casting holes on the flat wall of the 3D flexible welding platform casting should be reinforced with convex edges to reduce wall thickness;
2、The connection between casting walls should strictly prevent sharp corners and metal accumulation.The transition between thick and thin walls should be gradual,and sudden changes should be strictly prevented to avoid hot spots and stress concentration,which can lead to hot cracking,shrinkage,etc;
3、To ensure good formability of the welding fixture workbench castings,the small wall thickness of the castings should be controlled not to be lower than the allowable value.
4、Local thick sections of platform castings should be designed with excavated or cast hole structures as much as possible,and appropriately reinforced with added ribs;
5、The wall thickness of castings should strive for uniformity to prevent shrinkage and hot cracking.When determining the sequential solidification conditions,the wall thickness should be varied in one direction as much as possible.When determining the simultaneous solidification conditions,the wall thickness of equal cross-section should be made as much as possible;
6、The platform should try to avoid large horizontal surfaces inside the castings as much as possible;
7、The casting structure should be designed to allow for unobstructed shrinkage during cooling;
8、There should be several connecting columns for large interlayer cavities such as water and gas circuits in castings.
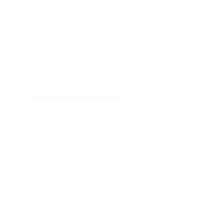
-
Welding Workbench Surface Thickness: Proper Thickness Selection and Comparison of Materials
2025-07-07 04:58:24
-
In-Depth Analysis of Load-Bearing Capacity and Stability of welding table: Ensuring Safe and Efficien
2025-06-18 12:14:47
-
welding table and Welding Efficiency Enhancement: Practical Methods for Equipment Optimization
2025-06-16 08:26:53
-
welding table and the Improvement of Welding Efficiency: Practical Methods for Equipment Optimization
2025-06-15 05:34:05
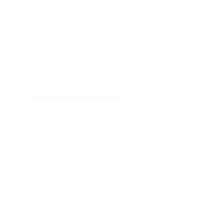
Whatapp:+86 18932785670
Tel:+86 18932785670
E-mail:project@haoranmj.com
Add:Across from Sanjing Distillery on Road 4, Botou Economic Development Zone, Cangzhou City, Hebei Province